INTRODUCTION
The Managing Directors of PUMA SE remain firmly committed to the 10 principles of the United Nations Global Compact, as well as the United Nations Guiding Principles of Business and Human Rights. We are committed to acting responsibly, be it with regard to our own employees, our business partners, consumers, the communities in which we operate or within our supply chain.
In 2017 we focused on creating a positive impact, firstly by integrating sustainability into the core business functions of PUMA via our company-wide 10FOR20 Sustainability Targets and secondly by taking an active role in industry-wide initiatives, such as the Sustainable Apparel Coalition and the Zero Discharge of Hazardous Chemicals Foundation.
We expanded our human rights due diligence process with a human rights assessment in our supply chain and created a heat map of potential risk areas.
We also moved our Global Stakeholder Sustainability Meeting to Asia, where most of our suppliers are based.
In addition, we published the results of our 2016 Environmental Profit and Loss Account, which summarizes the external environmental impact of our business activities in financial terms.
The execution of our 10FOR20 Sustainability Strategy continues as planned:
- The number of shared compliance audits with our industry peers doubled and the joint industry assessment tool from the Social & Labor Convergence Project, which will replace our own audit tool in the future, was piloted.
- The wastewater guidelines of the Zero Discharge of Hazardous Chemicals Foundation (ZDHC), an industry-wide initiative developed with other major brands, were implemented in 42 main factories. These guidelines will lead to a reduction of testing costs as well as clarity on what good wastewater treatment practices look like.
- In cooperation with several major brands and the International Finance Corporation (IFC) we launched our new supply chain climate change program aimed at promoting renewable and efficient energy consumption in our supply chain.
- The use of more sustainable materials, such as BCI cotton (40%), bluesign polyester (46%) and FSC certified paper and cardboard (92%), was increased and the use of solvent-free polyurethane was piloted.
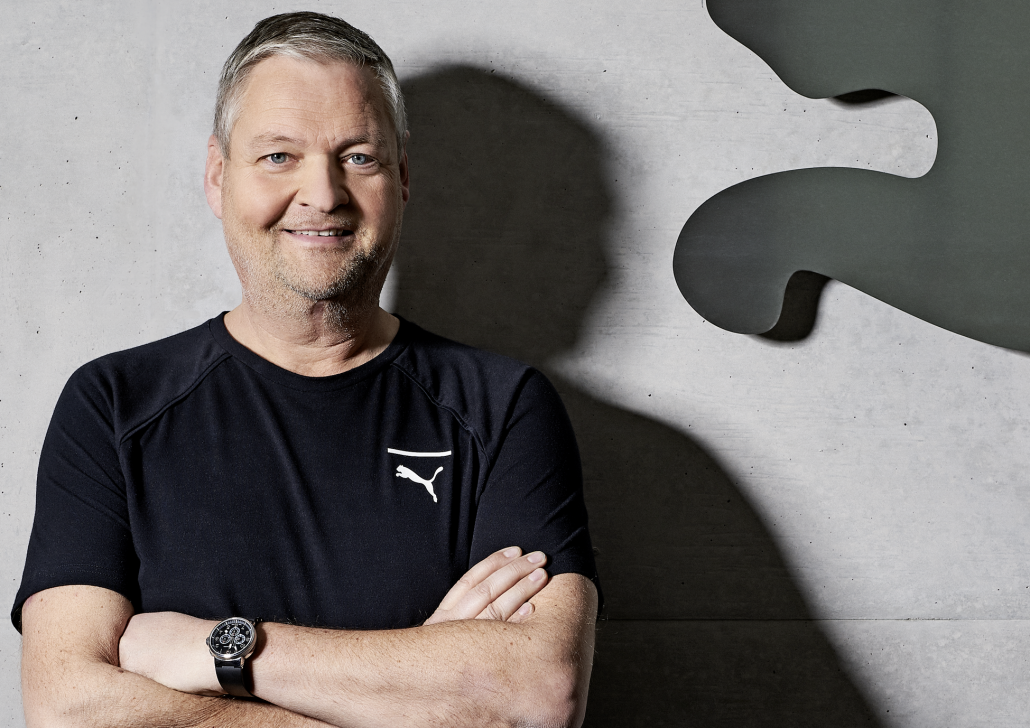
- The implementation of third-party risk assessments and training our quality inspectors on how to identify serious occupational health and safety risks during factory visits was a major focus in 2017. The importance of this was highlighted by a tragic fatal accident at a PUMA supplier in January. A new PUMA anti-corruption policy was implemented and 99% of PUMA employees with email accounts worldwide, as well as over 300 PUMA suppliers, were trained on this issue. We also included an anti-corruption section in our supplier audit tool.
Although we are happy with the overall progress towards fulfilling our 10FOR20 Targets, we are conscious that there is still much to do if we are to achieve our ambitious goals and meet the challenges we constantly set ourselves.
Yours sincerely,
Lars Sørensen
Chief Operating Officer PUMA
SOCIAL ASPECTS
HUMAN RIGHTS (10FOR20 TARGET NO. 2)
Zielbeschreibung:
Embed Human Rights across our operations and suppliers. Positively impact the communities where PUMA is present. Relevant to United Nations Sustainable Development Goals 3, 4, 5, 10.
Examples from the 10FOR20 Action Plan:
KPIs:
The respect for human rights has been at the heart of our sustainability strategy since it was first drafted more than 15 years ago. Today our engagement covers our own company sites and extends to our supply chain, forming a key principle of the PUMA Code of Conduct.
We report on code compliance at our supplier factories in the Social Compliance chapter. Positive community impacts are reported in the Human Resources section of this report.
This chapter focuses on the results of the Supply Chain Human Rights Risk Assessment conducted in 2017 with the specialist consultancy firm twentyfifty.
In 2017, we expanded our human rights risk assessment to the supply chain and took steps to mitigate the risks identified, for example in the area of cotton farming via our membership of the Better Cotton Initiative.
Based on the Human Rights Capacity Diagnostic (HRCD) developed by twentyfifty we have assessed our capacity to apply the human rights due diligence concept to our supply chain operations and to identify hotspots where further action is required.
The results show that PUMA is pro-actively embedding responsible business conduct in its management processes as well as collaborating with other peers and industry initiatives. On the other hand, practices regarding mapping and assessing risks and impacts in the lower tiers of the supply chain are still reactive and need to be better integrated at the strategic level.
Our social compliance program helps us to cover the first tier of the supply chain as well as core Tier 2 suppliers. We identified high risk areas in the field of cotton farming and cattle ranching as well as several blind spots, for example at ginneries, the lower tiers of leather tanning and marine shipping.
We discussed the results of our risk assessment with internal and external stakeholders and set up an action plan to mitigate the potential risk identified. It should be noted that these risks are endemic to these industries and will not be eliminated by the actions of a single brand.
In June 2017, we published our first PUMA Statement on Slavery and Human Trafficking, in accordance with the UK Modern Slavery Act.
In terms of capacity-building we launched a new women’s empowerment program, working with our global partner ILO Better Work at two key suppliers in Bangladesh.
Our PUMA Human Rights Action Plan is available on our website and we welcome stakeholder feedback via: sustainability.stakeholders@PUMA.com