Select Sections of PUMA’s
2018 Sustainability
Performance
In this year’s annual report, our sustainability section focuses on the topics that were highlighted as most important by internal and external stakeholders during our most recent materiality analysis.
Human Rights and Social Compliance
PUMA is defined not only by the products we create, but by the lives we improve. This not only applies to our customers, but also to our workers and the communities in which they live. We aim to ensure that our products are manufactured in workplaces where human rights are respected. On a daily basis, our global sustainability team (located in nine countries over three continents) collaborates with our manufacturing partners to improve working conditions, ensure workers are treated fairly, and certify that factory conditions meet safety standards.
We describe below our work and plans for improvement through our capabilitybuilding projects, audits system, worker feedback systems, and use of social key performance indicators across our suppliers.
Capability Building
Our capability-building initiatives are grounded in our endeavor to align our sourcing practices with the principles of sustainable development. PUMA works with suppliers on capability-building initiatives to build resilience and self-sufficiency in these areas. In 2018, our work included an expanded partnership with the International Labor Organization’s Better Work program in Bangladesh, training over 1,000 workers on issues related to women’s empowerment in the workplace. More broadly, we trained 315 PUMA suppliers at our annual supplier Round Table Meetings on how to avoid forced labor. This was done in collaboration with the International Organization of Migration, or other expert organizations, which highlighted the connection between recruitment fees paid by migrant workers in countries like Mauritius and Taiwan and potential forced-labor issues. Migrant workers are the group considered most exposed to significant risks of forced labor in supply chains.
PUMA adheres to the UN Declaration of Human Rights, the International Labor Organization’s Core Labor Conventions, and the ten principles of the United Nations Global Compact–these have been reflected in our Code of Conduct since 1993 and in our Code of Ethics since 2005. We will continue to build on this enduring commitment to improve the lives and working conditions of the workers we rely on.
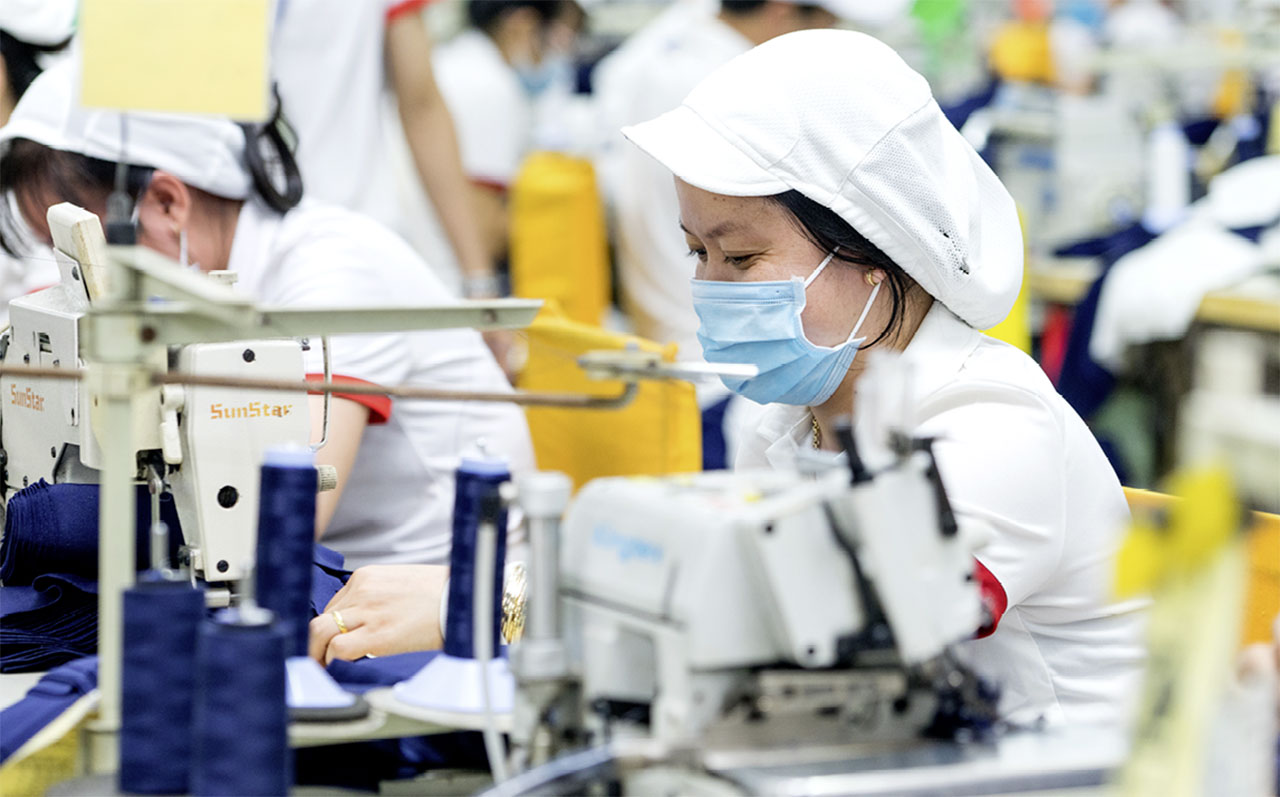
Audits
Social audits remain an important pillar of measuring human rights impacts as they illuminate areas for improvement across our supply chain. In 2018, we continued our partnership with the Fair Labor Association, the Better Work Program of the International Labor Organization and International Finance Corporation, and the Social and Labor Convergence Program (SLCP), supporting the rollout of the SLCP in China. Additionally, we engaged various regional organizations to ensure supplier compliance to international human rights and labor standards. As duplicative audits by numerous brands can create an administrative burden on a single vendor and be an inefficient use of resources, we heightened our collaborative efforts in this area to increase the percentage of shared audits with other companies from 27% to 39% of PUMA suppliers. In this way, we are enabling our value chain to receive two sets of benefits, reducing costs and resources and maximizing the efficiency of how we monitor our collective supply chain as an industry.
PUMA’s social audits evaluate the status of workers’ situations in areas such as freedom of association, health, safety, appropriate wages, fair treatment and working hours. In 2018, we continued to achieve nearly 100% compliance monitoring of our active Tier 1 manufacturing partners. We also audited our most important Tier 2 suppliers and piloted an audit in a PUMA warehouse.
In total, we conducted 536 audits in 473 factories with 94% of our Tier 1 earning a passing grade. Since the prior year, Tier 1 vendor compliance improved by 2%, continuing our positive trajectory. 6% failed to meet our requirements and if an active PUMA supplier, we worked with these partners to improve the situation. 47% received passing grades of those that received a second audit. Eleven factories could not sufficiently improve their performance and were consequently delisted from our active supplier factory base. Those that applied to be suppliers but failed their first audits were not admitted.
In 2019, we plan to further increase the passing grade within our T1 and core T2 suppliers to 95%.
Workers’ Feedback
Having the ability to articulate one’s needs and concerns is a key tenet of human rights. Providing workers with avenues to use their voices to advocate for themselves is a top priority for PUMA as part of our commitment to playing fairly as a market leader.
In 2008, we developed Worker Voice, a workers’ feedback system that enables vendor employees to share concerns in a confidential manner, as well as for outside parties to provide input to PUMA. The objective of Worker Voice is to understand if our sustainability initiatives create a positive impact for workers and effectively identify areas for further improvement. PUMA responds directly to concerns raised through this system and shares them with vendor management, upholding worker confidentiality, to take collaborative action and arrive at holistic and appropriate resolutions.
We are pleased to see that our efforts in 2018 have given our workers a platform for voicing complaints, advocating for their needs, and ensuring that their concerns are acknowledged. We expanded our Worker Voice coverage by including more than 4,000 workers who participated in a well-being survey among nine Chinese core suppliers through an app-based technology. In total, 44 workers across eight countries took advantage of PUMA’s feedback system, compared to 74 in 2017. Our team resolved all complaints raised, 5% more than the year prior. We also received three third-party complaints from external organizations related to PUMA manufacturing partners, after ten complaints in the year prior. Two external third-party complaints focused on the right to freedom of association and one focused on fair compensation. Of these, two were resolved and one is still pending a decision in local labor courts.
In 2019, we aim to keep our resolution rate for workers complaints consistently above 90% and resolve all third-party complaints.
Social Key Performance Indicators (S-KPIs)
Social Key Performance Indicators (S-KPIs) help us measure and report on important aspects of our business that affect worker health and safety, fair wages, and diversity and inclusion. These S-KPIs include:
- The average number of work accidents per 100 full-time employees
- Payment of workers at our manufacturing partners compared to
local minimum wages - Female representation among our workers
- Average hours of overtime work per week
- Coverage under social insurance provisions
- Percentage of fixed-term vs. permanent contracts
- Workers covered by a collective bargaining agreement
Table 4 shows that 95% of workers employed at our core suppliers are covered by social insurance. In addition, 68% have a permanent working contract, four percentage points more than in 2017. Over the last year, we have experienced improvements in the areas of overtime hours and coverage by collective bargaining agreements, by almost one hour less per week and five percentage-point increase respectively. These improvements have a direct impact on worker wellbeing and ensure that more of the people employed by our suppliers have access to the help they need, when they need it.
While PUMA does not measure the payment of a “living wage”, table 4 indicates that on average, our core suppliers pay 21% above legally mandated minimum wages in their respective countries. Adding overtime and bonuses, this increases to 84%.
Our plans for improvement are to further increase the percentage of permanent contracts and workers covered by social insurance over time, while maintaining an average salary structure well above minimum wages.
We will also continue to highlight the importance of freedom of association and collective bargaining as an enabling right for all other labor standards.
Reducing Impacts on the Environment
By making intentional business decisions about what we produce and how, we strive toward our target to provide people with a planet in which they can play. Climate change threatens our ability to live well in the long term, because it threatens the health and availability of the natural resources we enjoy today. Our customers can only be athletes when they have clean air and water, and a field on which to compete. According to the Intergovernmental Panel on Climate Change (IPCC), even if overall global warming is limited to below two degrees Celsius as agreed by the United Nations in Paris, there will still be wide-ranging consequences for low-lying regions, human health, and the health of our ocean ecosystems, where those hardest-hit are likely to be some of the world’s most vulnerable communities.
At PUMA, we believe in doing our part to contribute to a healthy ecosystem for all to thrive in. We summarize below our current work and future plans for addressing climate change, materials use, sustainable product design, sustainable packaging, water use and chemicals management throughout our supply chain.
PUMA’s sustainability strategy focuses on reducing our own carbon emissions through the following measures:
- The use of energy efficient vehicles, buildings and devices
- The direct purchase of renewable electricity where available
- The purchase of renewable energy certificates where a direct purchase is not feasible
We are aiming to reduce carbon emissions within our supply chain through the following additional initiatives:
- Working with logistics service providers who are leaders in fighting climate change
- Energy efficiency programs for our core suppliers
- Supporting selected suppliers to invest in renewable energy creation
- Switching from conventional to more sustainable raw materials
- Engaging with our industry peers for industry-wide climate solutions
Environmental Key Performance Indicators (E-KPIs)
We hold ourselves accountable to our sustainability strategy by collecting and publishing data on the average water consumption, CO2 emissions, and waste for finished goods manufacturing within our major product categories. These Environmental Key Performance Indicators (E-KPIs) allow us to quickly evaluate the results of our actions in finished goods manufacturing.
We are pleased to report that we have made clear improvements on all reported E-KPIs since our baseline year 2015. The reductions in CO2 emissions as well as energy and water usage per piece or pair produced show that our multiple energy efficiency programs and consistent reporting of core suppliers have generated positive momentum, eliminating unnecessary consumption and increasing energy and water efficiency. In addition, a number of our suppliers have already switched to or installed renewable energy sources, including bio-mass boilers and solar photovoltaic panels at their facilities.
In addition to finished goods manufacturing, we are also working with our major materials suppliers on reducing their environmental impact and improving their resource efficiency.
The next tables provide average consumption figures for the manufacturing of textile fabrics and leather. We use these figures to benchmark our fabric and leather suppliers over time and against one another. This helps us to prioritize those suppliers for efficiency programs, where we expect to achieve the largest impact.
Sustainable Product Design and Development
We believe that the use of more sustainable materials is crucial for designing and developing products that both anticipate evolving consumer demand and facilitate more environmentally resilient consumption. In 2018, we re-emphasized the need for our teams to design and develop more sustainable products. Utilizing our PUMA Sustainability-Index (S-Index), our benchmark for more sustainable products, we have encouraged our product team to significantly increase the use of more sustainable materials in their collections.
This year also saw the launch of new collaborations with ASOS, the British fashion and retailer, and SONRA, a German footwear brand that creates shoes from sustainably tanned leather. Both product lines emphasize local sourcing and production to minimize the distance to market (reducing emissions relating to transport of materials and goods). Furthermore, in the case of the collaboration with ASOS, emissions from the production phase were offset with a renewable energy project established in Turkey, rendering the line effectively carbon-neutral.
Sourcing and Efficient Use of more Sustainable Product Materials
Consumer and environmental trends over the past year have underscored the importance of responsible sourcing and manufacturing to provide customers with high-quality products whose origins reflect the values of those who use them. PUMA has continued to push its longstanding commitment to these values to enable a smooth transition to sourcing sustainable materials. Although these resource expenditures and associated negative impacts from producing raw materials are embedded in the operations of our partners, we continue to reach deep into our supply chain to achieve better environmental outcomes. Sourcing better materials helps reduce and avoid operations that accelerate environmental challenges, such as heavy water consumption, CO2 emissions, pesticide damage to ecosystems, animal cruelty, and harm to human health.
As part of our 10FOR20 Sustainability Strategy, we established ‘volume targets’ for sourcing more sustainable versions of key product materials, including cotton (Better Cotton Initiative or organic) and Polyester (bluesign® or Oeko-Tex®-certified, or recycled). Our efforts since 2015 have enabled us to meet our targets two years early (notably, the target for sustainable leather and FSC cardboard sourcing was 90%). This early achievement provided us with the opportunity to level up our ambition, so we increased our target for both more sustainable cotton and polyester sourcing by 40 points to 90% of our total procurement for both materials. We continued to aim higher by adding a new global volume target for Responsible Down Standard-certified down feathers (90%), as well as for better (i.e. solvent-reduced) polyurethane (500,000 pieces).
Alone, the 10,370 tons of BCI-certified cotton we used in 2018 will enable water expenditure savings during cotton farming of between 3% and 20%, depending on the regions where the farming takes place. At an average water consumption of ten cubic meters per kilogram of cotton, even a 3% savings amounts to 3.1 million cubic meters of water saved, an amount capable of filling approximately 15 million bath tubs.
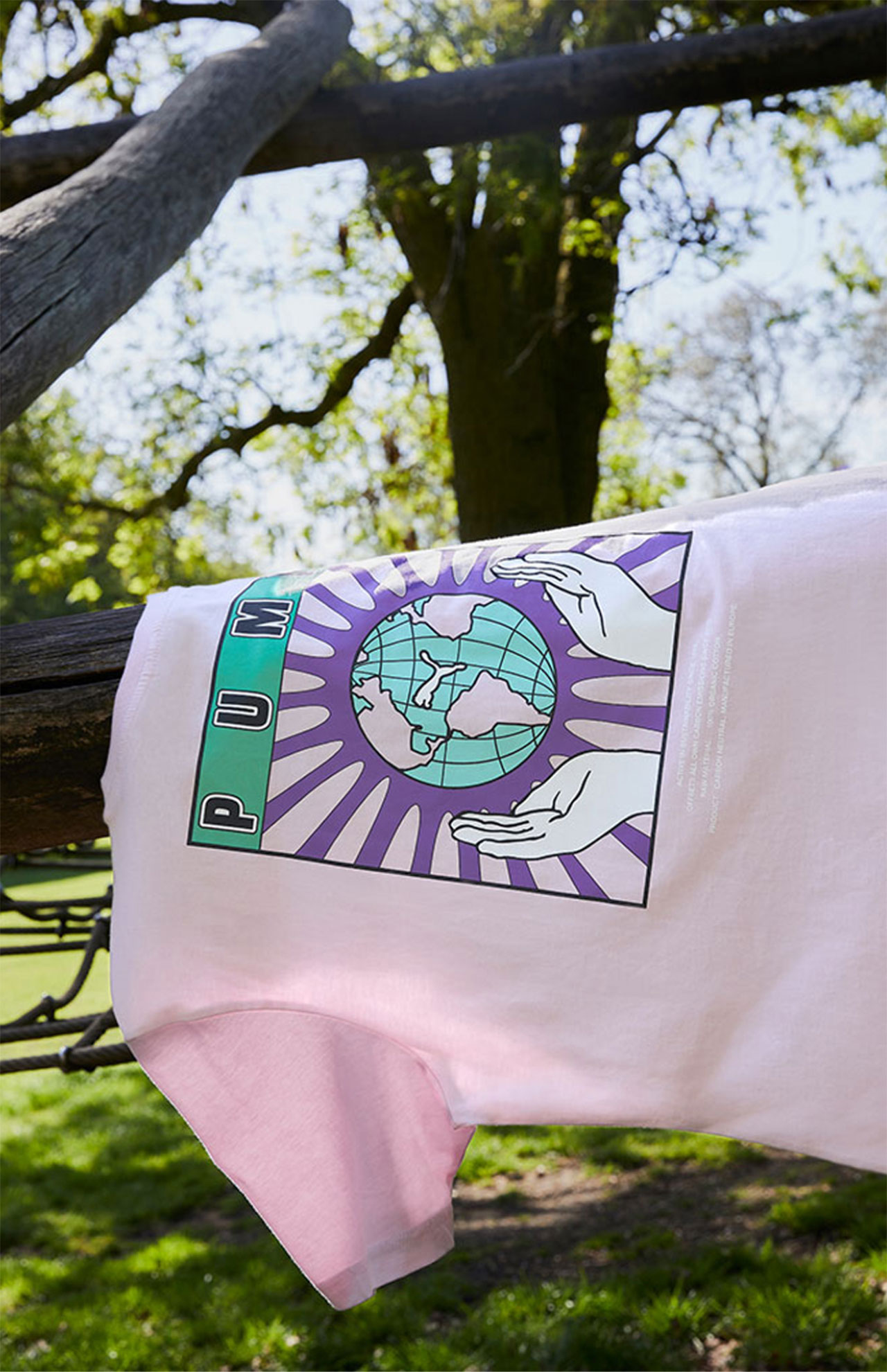
Maximizing Resource Utilization
Our industry needs to redefine the concept of “waste”. Our more sustainable product strategy also includes the reduction of waste created during the production process, through more efficient use of resources. The result is a more streamlined consumption of raw materials that lightens our environmental impact. We are discovering and innovating around new ways to take material ‘waste’ that would otherwise be discarded and reincorporate it back into the production of PUMA products. For example, small pieces in the ‘first run’ of producing footwear soles can be melted together for a different collection or put into packaging or components of other products. This reduces the contributions to landfills, which emit methane, a greenhouse gas, and directly contributes to climate change.
In 2018, we continued to develop initiatives with suppliers to discover and implement the reusability of waste materials in production processes. This begins with front-end design and development decisions, such as our renewed focus on expanding S-Index product requirements to including recycled materials. Our objective has been to find simple and feasible solutions for production processes that create a net benefit in terms of environmental impact, where reincorporating reusable material is not excessively laborious or energy-intensive.
More Sustainable Plastics and Packaging
2018 brought new insights into how ocean plastic pollution and microplastics may endanger human health, ecosystems, and the wildlife that relies on them. Given the potential consequences of plastics in the environment, our responsible use of polyester, polyurethane, and polyethylene is a top priority for PUMA. The topic has been as well raised as relevant issue for PUMA by a variety of stakeholders, including environmental NGOs, own employees and customers.
Following is a summary of actions taken in 2018 with regard to polyester, polyurethane, polyethylene, as well as streamlining our cardboard packaging and hangtags. Together, these efforts aim to reduce the impact that PUMA’s plastic usage generates, which helps protect forests, and leads to less ocean pollution and lower volumes of landfill waste. In many cases, this also reduces our costs, making what is best for the environment, best for our business.
Polyester used on PUMA products: Polyester is the most widely used plastic-based material across PUMA product lines.
- We increased our 2020 target of sourcing certified sustainable polyester by 40 points to 90%. Our 2018 actual level of sourcing was 86%, taking into consideration bluesign®, Oeko-Tex® and recycled polyester certifications.
- PUMA established plans to join a research program on microfibers in early 2019 to explore how we can best take action in this area to make significant positive impact. This builds on our participation in related industry meetings and our own efforts to closely follow existing and emerging research.
Polyurethane used on PUMA products: Polyurethane is widely used on PUMA shoes and accessories.
- In 2018, we initiated sourcing for better (solvent-reduced) polyurethane, to reduce the amount of dimethylformamid or DMFa, a chemical that is widely used in conventional polyurethane processing.
Polyethylene used for bags and packaging:
- All PUMA retail stores have completed implementation of bans on the use of plastic bags.
- For our outlet stores, any plastic bags used must contain at least 80% recycled content (effective beginning of 2019).
- We have worked to reduce the thickness of polybags (used for packaging PUMA apparel and accessories) to decrease the use of polyethylene.
- We continued our research on replacing polyethylene with a more sustainable material.
Footwear packaging and hangtags:
- We ensured the PUMA shoe box, primarily cardboard and paper, continues to be made of 92% recycled paper content and certified by the Forest Stewardship Council (FSC©).
- Our cardboard-based hangtags are also fully FSC©-certified.
CO2 Emissions
In line with the United Nation’s Paris Agreement, PUMA is committed to contributing its fair share to limit global warming to well below two degrees Celsius. In 2019, we will continue our development of a science-based CO2 emissions target. In the interim, PUMA established an internal target of 3% reduction relative to sales. This ensures that we continue to take goal-oriented actions. To check our pace toward the 3% reduction milestone, the first step is tracking CO2 emissions–which also helps identify key areas to make significant changes in our supply chain, both in our direct operations and in those of our supply chain partners.
The scope of our CO2 emissions tracking includes key environmental performance data for PUMA offices, stores and warehouses, and from business travel. Reaching deeper into our supply chain, we also include emissions from Tier 1 suppliers and transport partners. In summary, 2018 saw a 5.3% combined reduction of tons of CO2 per million euros of turnover per year over the year prior. This equals 3.3 tons of CO2 per million euros of turnover per year which is equivalent to over 3,000 passenger cars taken off the roads.
We were able to reduce our emissions relative to sales for our own offices, stores and warehouses, for example by abandoning an old and less efficient building at our headquarters. We also reduced the emissions from the Tier 1 suppliers of our goods as described on table 5.
However, we also recorded an over-proportional increase in airfreight caused by the increased volume of goods produced and shipped, as well as a substantial increase in business travel. In 2019, we will work on reversing the negative trend in those two areas.
Water Use
The access to clean and safe water is a fundamental human right. Availability of adequate clean water is essential for health as well as social and economic development.
We recognize that industrial water consumption comprises 22% of global water use as per findings by the United Nations, which underscores our opportunity to make a positive difference toward higher availability and water quality in local communities and on the ecosystems on which they rely. In 2018, we stepped up our commitment and delivered better results in the areas of water efficiency and wastewater management to achieve improvements in the communities where PUMA products are made.
Water Efficiency
In 2018, we continued a collaboration with the World Bank’s International Finance Corporation on running programs focused on water efficiency (as well as energy efficiency and climate-change performance). Through this partnership, we established two resource efficiency programs with eleven core factories in our major sourcing countries, Vietnam and Bangladesh. Those programs enable participating factories to undergo a detailed resource efficiency audit, followed by proposals on how to improve their efficiency in a cost-effective way. Frequent reporting and help from the IFC to identify the right finance tools for implementation round out the program’s scope.
Ongoing benchmarking and the phase out of ineffective suppliers have led to an average reduction of water use in finished goods manufacturing of 33% for footwear and 38% for apparel between 2015 and 2018 see tables 5.
On Tier 2 or the material supplier level, we have not yet been able to replicate these savings. However, we have started to measure water consumption from Tier 2 suppliers and hope to realize resource efficiency gains in the coming years.
Wastewater Management
Textile production requires large volumes of water as a solvent for chemicals and dyes as well as to wash and rinse products. This series of operations is known as wet processing. PUMA focuses water efficiency efforts on facilities with wet processing operations as they represent the most water-intensive stage of production. Because wet processing typically occurs at the material supplier level (Tier 2), we include major suppliers from this category in our wastewater testing program to comprehensively understand the impacts of our supply chain.
Firstly, compliance with relevant national wastewater standards is a precondition for all suppliers interested in conducting business with PUMA. Ensuring wastewater standards is thus a required component of our frequent PUMA compliance audits conducted for all potential and existing suppliers globally.
The PUMA wastewater testing program is aligned to the wastewater quality guideline of the Zero Discharge of Hazardous Chemicals Foundation (ZDHC), which was developed and published with the help of PUMA in 2016. Since its inception, we have been able to consistently increase the scope of the program, from 33 suppliers in 2015 to 58 in 2018.
Testing includes both traditional wastewater parameters and hazardous chemicals and includes 183 different chemicals. A failure within one single parameter leads to a non-compliant rating. The results show that heavy metals are hardly found in the wastewater of our wet-processing supply chain. Regarding priority hazardous chemicals, the compliance rate improved from 67% in 2017 to 71% last year, meaning that seven out of ten suppliers did not find any such chemicals in their wastewater. For conventional wastewater parameters, such as pH value, biological oxygen demand or color, we still see room for improvement, despite a minor increase in compliance rates from 48% to 52%. While typically not toxic, the release of colored or hot wastewater can still have a negative effect on the receiving water body and local environment.
In 2019, we will use the experiences gained from two years of wastewater testing according to the ZDHC guideline to work with those suppliers whose compliance rates remain below our standards. Training programs developed by the ZDHC, and used across ZDHC member brands, will assist us in this effort.
Health, Safety & Chemicals Compliance
Our commitment to health and safety is foundational to how we operate and a guiding principle that informs our supply chain partnerships. Our view extends from the suppliers’ employees, the local communities in which PUMA operates and consumers. We demonstrate this by exceeding local legal requirements when required to reduce the negative impacts of chemicals used in our supply chain in the communities we serve. We also adhere to the highest legal standards for product safety in all countries in which we operate.
While the effects of potentially hazardous chemicals on human health have yet to be completely assessed, PUMA takes precautionary measures to prevent potential harm to human health and the environment from its products and operations. These measures include supporting working groups with industry peers to further research the topics and better management of natural resources used in operations.
Furthermore, to facilitate our chemical sustainability strategy, PUMA has adopted the Restricted Substances List of the AFIRM Group, and the Manufacturing Restricted Substances List of the ZDHC.
Both groups work as industry leaders on chemical management best practices. This provides us not only with the industry standards for streamlining our processes, but also gives us the opportunity to coordinate alongside other members in our industry on which chemicals we use, enabling greater and more systemic impact within global supply chains. We mandate that all materials used for PUMA products be tested in accordance with our Restricted Substances List (“RSL”) before the start of production in independent and accredited third-party laboratories.
Table 13 provides an overview of the RSL testing results and certifications between 2015 and 2018. We are pleased to report compliance rates of over 97% for all product divisions in 2018, with an average compliance rate of 98.1%, representing a 6.2% improvement over the 2015 average.
In addition to our materials testing program, PUMA also conducts random testing of finished products to confirm full compliance with legal requirements and the AFIRM Restricted Substances List. During 2018 our random testing confirmed full compliance of all tested products.
Phase Out of Hazardous Chemicals
PUMA is committed to supporting the global agenda of managing chemical use carefully – especially for those that are considered hazardous – as well as to phasing out those that raise health-related or environmental concerns.
In 2011, PUMA made a historic commitment to eliminate priority hazardous chemicals from our supply chain, co-founding the Zero Discharge of Hazardous Chemicals (ZDHC) Foundation initiative. That same year PUMA was the first company to agree to a public “Detox” commitment with Greenpeace. We agreed to proactively phase out hazardous chemicals, not only from finished PUMA products, but also from the production cycle across our global business. In our continuous pursuit of this goal, we have partnered with several industry peers to implement a Manufacturing Restricted Substances List, using standards developed by the ZDHC.
We are proud of our progress on the phase-out of two major hazardous chemicals groups in 2018. First, perfluorinated chemicals (PFCs), typically used for water-repellent coatings, are considered environmental contaminants, because they fail to break down once they have been used.
In addition, they disrupt normal chemical processes in living things and can have negative effects on immune function. We are happy to announce that we have completed this phase-out and that PUMA products are now PFC-free.
We also worked on our long-term reduction of organic solvents or volatile organic compounds (VOCs) in footwear production. Since VOCs easily evaporate, exposure can occur through inhalation and lead to negative health effects for workers in footwear factories. VOCs can also cause an unpleasant smell in products.
A reduction in the use of VOCs therefore protects both workers and consumers. Our efforts demonstrate steady improvement over recent years, reducing consumption per pair of shoes from 40.2 grams per pair in 2010 to 17.7 grams per pair in 2018. This result falls below 18 grams per pair for the first time, meeting the EU Eco Label requirement. We are encouraged by this success and confident that we are on track to achieve our target of 15 grams per pair by 2020.