Human Rights
Target Description:
- Train 100,000 direct and indirect staff on women’s empowerment
- Map subcontractors and Tier 2 suppliers
- Two hours of community engagement per FTE globally per year
Relates to United Nations Sustainable Development Goals 3, 5, 8 and 10
KPIs:
- Percentage of worker complaints resolved
- Number of factories with an A, B+, B-, C or D grade
- Number of Tier 2 suppliers and subcontractors included in our risk mapping
- Number of zero-tolerance issues prevailing at year end
- Number of employee hours spent on community engagement (KPI shared with Human Resources)
- Number of workers trained on women’s empowerment
PUMA’s sustainability policies are aligned with the United Nations’ (UN) Declaration of Human Rights, the UN Guiding Principles (UNGPs) on Business and Human Rights, the International Labor Organization’s Core Labor Conventions, and the ten principles of the UN Global Compact (UNGC). Observing Human Rights was part of our first Code of Conduct developed in 1993 and has guided our business ethics ever since. It has been the long-standing practice of PUMA to monitor our supply chain and conduct Human Rights due diligence for our suppliers globally, including those in major production hubs, such as Vietnam, Bangladesh and China continuously and rigorously.
Human Rights at PUMA'S own entities
Guided by our Code of Ethics and Code of Conduct, PUMA’s company culture of diversity and inclusion puts Human Rights at the centre of everything we do. Our commitment to employee well-being is also documented in numerous employee awards and top-employer rankings received all over the world.
Our internal programmes to uphold Human Rights include measuring gender, nationality, and age distribution among our colleagues, providing a safe work environment as well as elected worker representatives and collective bargaining agreements at selected larger offices, such as our German headquarters. In December 2023, PUMA appointed a Human Rights Officer to monitor PUMA’s risk management system, risk analysis relating to human rights and compliance with Human Rights due diligence regulations. In addition, we worked on a Human Rights Handbook for our own entities globally, to be published in 2024.
All PUMA employees who feel that ethical standards in business may have been compromised can raise their voices. Various channels are in place to report any suspicions and/or observations related to modern slavery or other Human Rights aspects. In practice, all employees can address their requests regarding apparent failures to their line manager. They may also raise the matter with staff representatives, the Legal department, the Internal Audit department, or via a toll-free external whistleblower platform available worldwide. Our Ethics Committees make sure that no action is taken against an employee who, in all good faith, reports a case of failure to comply with an ethical principle of the Code of Ethics, because of having reported the matter. In 2023, to meet its obligations under the German Act on Corporate Due Diligence Obligations in Supply Chains (LkSG), PUMA published its Rules for the Complaint Procedure.
Reform Initiative
As REFORM continues through its fifth year of existence, our partnership with The Trevor Project (TTP) continues to drive impact in our communities with a focus on supporting policies and practices that affirm and protect young LGBTQ athletes. In 2021, in partnership with TTP, we sought to build a well-researched and comprehensive training scheme to support equity in sports and promote gender inclusivity. In 2023, we launched the Reform the Locker Room programme, furthering our reach to locker rooms, classrooms, and offices alike.
REFORM was also able to launch a new project and collection, called Icons of Unity. Icons of Unity honors PUMA ambassador and global Icon, Tommie Smith, and amplifies his message of Justice, Dignity, Equality and Peace. As we continue to build out this programme, we look forward to identifying athletes, colleagues, and community leaders who embody this characteristic of Tommie, being more than what is obvious and a beacon for a more united community. We kicked this off with an amazing interview with Tommie and Olympians, Felix Streng and Colin Jackson.
In 2023, we educated and preserved culture and history through our work with BLACK FIVES and its NY RENS 100 collection launched in November with court refurbishments and street dedications. We have been able to advocate for and amplify a message of rebuilding communities in conjunction with our partner Game of Our Lives and football star and PUMA ambassador Oleksandr Zinchenko and his Game4Ukraine charitable celebrity soccer match that raised large amounts of money to support the rebuilding of Ukrainian schools. We supported the match with game balls and training gear for all participants. We also hosted a match viewing event at our Herzo HQ with many of the Ukrainian families that have been relocated during the time of war.
REFORM continues to show up and show out for our broader communities and remains true to our brand vision; “…where all barriers to participation are removed so that everyone who wants to play can play.”
More on our Reform Initiative can be found here.
PUMA x BLACK FIVES collection which honours the 100th anniversary of the Harlem Rens. A panel discussion on Gidra, an Asian-American student-led newspaper created to stop the anti-Asian sentiment in 1969.
COMMUNITY ENGAGEMENT
Our goal is to reach a total number of hours spent on community engagement equal to twice our annual average FTE (full-time equivalent). We encourage all our employees around the world to participate and record projects and employee engagement on an online platform.
Our Community Engagement Programme has continued to create a positive impact locally by supporting social, health and environmental causes, and we were able to donate 57,000 community hours in 2023. Since 2017, we have now recorded over 200,000 community engagement hours globally.
For more information on PUMA's employee policies and philanthropic donations please refer to the Our People section.
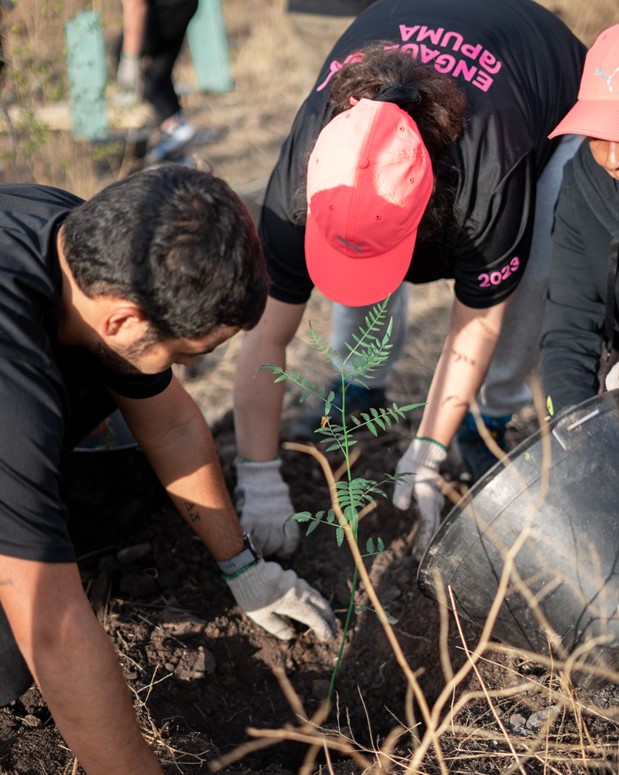
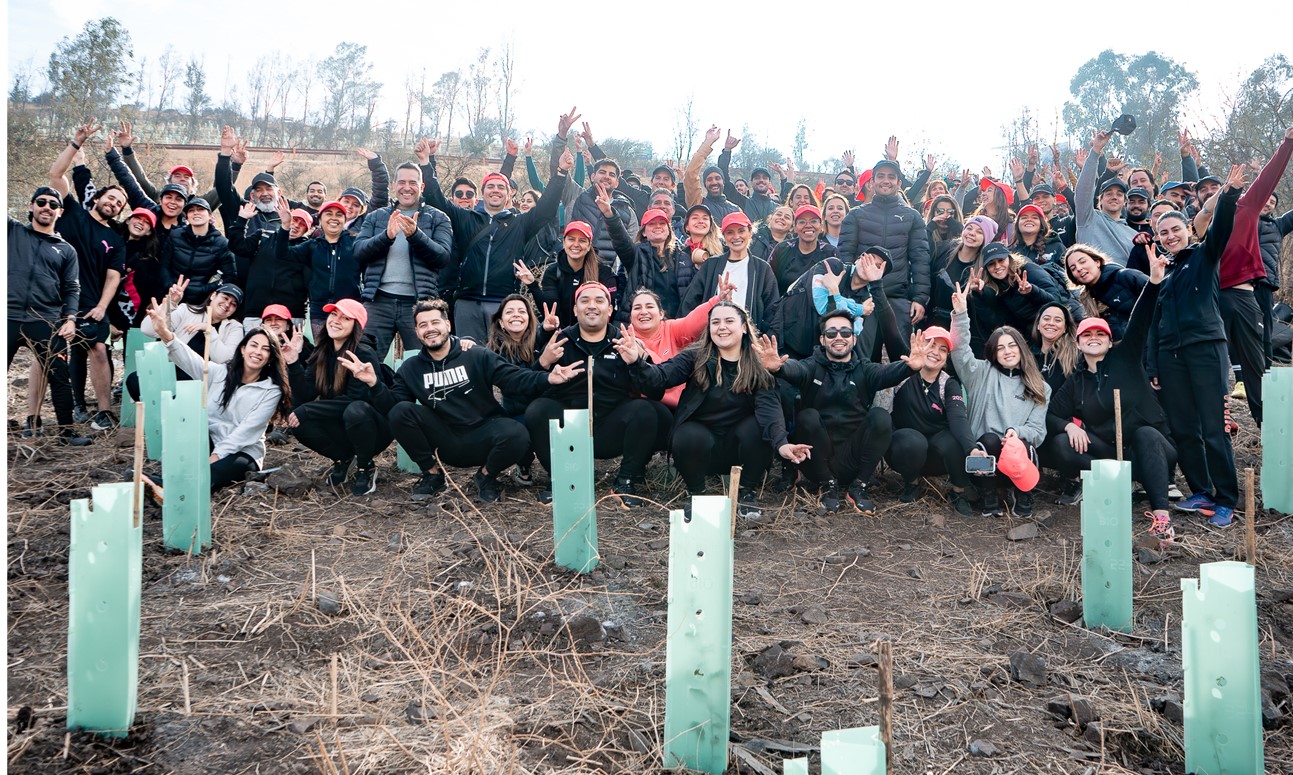
Community engagement activities from PUMA Chile: Reforestation in Renca
Human Rights IN THE supply chain
RESPONSIBLE PURCHASING PRACTICE POLICY
As a responsible business partner for our suppliers, we recognise that our business practices, and our trading terms and conditions can have a significant impact on the organisation at our suppliers’ factories. PUMA’s Responsible Sourcing Policy aims to reduce potential negative impacts. PUMA’s Responsible Purchasing Practice Policy was developed in 2019 to create a framework for guiding decisions and maintaining consistency through eight key principles:
1.Only working with suppliers that have signed a Manufacturing Agreement.
2.Payments to suppliers are made on time and in full. We only deduct payments and impose penalties when it is lawful to do so.
3.Price paid for the product to include reasonable labour costs, such as overtime premium payments, social insurance payments, and costs to comply with environmental standards.
4.Open production capacity must be declared by the supplier based on standard work weeks as per the law of the relevant production country.
5.Seasonal production plans are allocated considering the negotiated capacity with the supplier.
6.Sufficient production lead time must be provided.
7.Suppliers may not subcontract production without authorisation from PUMA. All subcontracting units should respect our Code of Conduct.
8.A minimum notice of six months must be given when ending a partnership or downscaling orders. Longer timeframes will be granted, based on the average production capacities used in the last two to three years, to reduce the impact on workers.
In 2022, 280 PUMA staff and 1,145 supplier participants received Responsible Sourcing Practice training. The training referred to the UN Guiding Principles on Business and Human Rights, to explain the link between the purchasing practices, potential impact on working conditions, and the risk of Human Rights violations.
In 2023, as part of our Due Diligence Policy review, we added a clause on responsible disengagement into our responsible purchasing practices. Following the Fair Labor Association guidelines, PUMA commits to provide a minimum of six months of notice when significantly downscaling orders or terminating a business relationship with suppliers. To mitigate impact on workers’ jobs and give suppliers time to find new buyers, a longer timeframe shall be granted, depending on the average production capacities used over the last two to three years.
Better Buying Survey
In 2023 we asked 32 strategic Tier 1 suppliers (11 accessories, 12 apparel, and nine footwear suppliers representing 69% of our business volume and 80% of our business value) to participate in the Better Buying survey to collect feedback from our core suppliers on the implementation status of PUMA’s responsible purchasing practices. 28 suppliers responded, and the response rate was 90.3%.
Better Buying gathers data from suppliers to provide guidance to brands for improving purchasing practices. Brands voluntarily invite their suppliers to participate. Suppliers rate their brands anonymously according to the five principles of responsible purchasing which focus on the buyer purchasing practices that could have the biggest impact on suppliers’ businesses:
1.Visibility: Brands provide enough information about the planned business for suppliers to act
2.Stability: Brands give suppliers steady and predictable business across the year
3.Time: Brands provide enough time for suppliers to complete all processes
4.Financials: Brands use fair financial practices with suppliers
5.Shared Responsibility: Brands play their part in improving supply chain social and environmental sustainability
We benchmarked our 28 suppliers' feedback with more than 800 suppliers' feedback from the 16 brands classified under sporting goods and discussed these results internally to set a clear focus area for improvement. PUMA’s overall score slightly increased in 2023, mainly due to the increased score on covering cost for compliant production, accountability for delays, regular forecast updates, and order cancellation percentage. The feedback is described below.
Visibility
Design and development can play a significant role in improving supply chain sustainability. Choices made at this stage have significantly lower financial, social, and environmental impacts. While all our samples are based on a tech pack, tech packs have also been reviewed in 2023 to improve the accuracy of information. PUMA has also provided internal training on the importance of providing accurate information to suppliers. Our purchase order accuracy has improved compared to 2022. Our suppliers recognise our efforts in increasing the use of more sustainable materials, 3D sampling, industry certification, and setting target prices before product development. Our sample hit rate remains strong.
All our suppliers confirmed that we provide them with a business forecast, enabling them to plan the workforce that is needed. In 2023, PUMA discussed its production capacity and the potential impact of forecast inaccuracies on suppliers. We also provided internal training for key business departments involved. PUMA has also been working with its suppliers to ensure their production capacity is accurate and there has been regular feedback on sales forecast to its sales division. Although the overall score has improved for 2023, we have identified the need to better communicate our overall forecasting and planning timelines and processes to our suppliers and improve in-season communication for some product divisions. Given the global macroeconomic situation in 2023, which has led to a change in customers' ordering behaviour, the gap between the placed and planned capacity results in unutilised capacity and excess material increased according to our suppliers.
Stability
We value long term relationships with our suppliers. 40% of our suppliers have been working with PUMA for more than ten years. To help ensure stability, as a principle, we will not cancel orders and accommodate order placement to respond to suppliers’ difficulties such as lockdown periods. In the case of order cancellation which remains less than 1% for PUMA, we always pay our suppliers for any liability associated with cancellations. In 2023, 100% of suppliers from Accessories and Footwear reported no order cancellation, while some Apparel suppliers reported cancelled orders.
Time
A large majority of our suppliers confirmed that we have an agreed time and action calendar for preproduction and production deadlines. In 2022 we received feedback from our suppliers that PUMA missed some deadlines, however through better communication in 2023, our suppliers confirmed an improvement.
Financial
Most suppliers feel they have favourable financial terms through digital payment, the FOREVER. BETTER. Vendor Financing Programme and through receiving payment for samples and bulk production in a timely manner. PUMA International Trading and the vendors have enabled the digitisation of the supply chain creating transparency, operational efficiency, and reducing complexity. For example, all payments to vendors are automated and paper-free.
We do not apply late penalties to our vendors, and suppliers confirmed we are flexible and accountable for delays. We will strengthen our communication of payment terms to suppliers. We also see opportunities to collaborate with our suppliers to increase their production efficiency related to style allocation, volume, standardisation of fabrics, labelling and packaging processes, etc. We made significant improvements in covering costs for compliant production compared to 2022, but suppliers also reported pressure in cost negotiation in 2023. Our suppliers also recognised our efforts to reduce audit duplication which benefits them in saving cost.
Shared responsibility
All our suppliers recognise that sustainability is the precondition for doing business with PUMA. However, in 2023, suppliers felt less incentivised to reach the sustainability goals compared to 2022 since we saw a decline in orders in the first half of the year and stabilisation during the second half. The majority of our suppliers acknowledge our effort to enforce our sustainability standards.
FOREVER. BETTER. VENDOR FINANCING PROGRAMME
The programme, established in 2016, allows suppliers with a good or very good compliance rating to benefit from PUMA’s high credit rating and preferred interest rates. The programme runs in partnership with IFC, BNP Paribas, HSBC, and Standard Chartered Bank.
At the end of 2023, 72 vendors were registered users (compared to 71 at the end of 2022). The financed volumes in the full year 2023 amounted to $ 478 million (-$ 322 million compared to 2022), which reflects the massive interest rate and with this financing cost increases for our suppliers, who chose other sources or tried to avoid external financing.
HUMAN RIGHTS RISK ASSESSMENT
In previous years we have conducted Human Rights risk assessments at corporate and the supply chain level and shared the results in our 2016 and 2017 Annual Reports. In 2021 we commissioned and completed a Human Rights risk assessment, focusing on forced labour management in the supply chain.
In our Handbooks, we request our vendors to conduct due diligence. To increase transparency, we report on the most common audit findings, training, grievances, and mitigation measures as outcome-focused key performance indicators (KPIs) to track the effectiveness of our supplier programmes.
The PUMA hotline is accessible to Civil Society Organisations (CSOs) and external stakeholders, including stakeholders representing vulnerable groups: women, children, migrant workers, indigenous people and national or ethnic, religious, and linguistic minorities. We also extend the scope of our social monitoring programmes to EMEA factories, high-risk countries warehouses, and to some non-core Tier 2 suppliers.
In 2023, we conducted a review of our grievance mechanism, in line with the UNGP criteria for operational-level grievance systems. To do this, we surveyed 14,823 workers at 45 factories in eight countries. The legitimacy of the PUMA hotline was acknowledged by 94% of workers, accessibility confirmed by 80% of participants together with 92% regarding the hotline's availability in a language they understand.
In 2023, we developed a Civil Society Organisations (CSOs) engagement policy to engage with them reactively and proactively. Please refer to the Due Diligence and Risk Assessment section of this report for more information.
risks
The most salient risks to human rights are forced or bonded labour in the supply chain and, at the farm level, child labour.
Freedom of association
As per World Governance Indicators (WGI), PUMA’s main sourcing countries have been identified as risk countries on the Voice and Accountability indicator, which measures freedom of association. Social conflict and freedom of association breaches could be a risk due to a lack of social dialogue at factories. The risk could be more upstream in our supply chain when no audit programme is in place or when there is no monitoring programme at the raw material extraction stage. We support our core Tier 1 suppliers to set up effective social dialogue platforms in factories and adopt certification such as Better Cotton and the Forest Stewardship Council to address raw material extraction Human Rights risks.
ILO Freedom of Association Committee has been investigating cases reported by International Trade Unions on allegations of retaliation, anti-union discrimination and dismissals, and the arrest and detention of workers for having participated in strike action, in a context where the legislative framework inadequately ensures the effective recognition of freedom of association, in Bangladesh and Cambodia.
In Bangladesh and Cambodia, there were third-party complaints related to freedom of association (described in the grievance section). As a countermeasure, all our factories in Bangladesh and Cambodia are enrolled in the ILO Better Work programme, which provides advisory services and supports factory management to create a participation committee as a platform for social dialogue.
Discrimination, sexual harassment, and gender-based violence
The Global Gender Gap Index measures gender equality in 153 countries by tracking and ranking a range of gender-based gaps across society. East Asia is ranked as medium, while South Asia is ranked lower. While East Asia has been able to reduce educational gender gaps, South Asia is one of the regions where women are the most disadvantaged in the workplace.
Social dialogue can be used as an effective tool to overcome the under-representation of women and promote gender equality at work. We support our core suppliers in setting up effective social dialogue platforms in factories that include women's voices. We also support them in conducting women empowerment training for factory workers.
Health and Safety
South East Asia is prone to natural disasters, disease outbreaks, and health risks related to climate change. In addition, building and fire safety risks have been identified as major risks in the apparel sector, especially in Tier 1 and Tier 2 facilities. One of the World Health Organization’s key priorities is to strengthen emergency risk management for sustainable development and to promote health coverage and robust health systems.
We maintain a high focus on the OHS performance of our core Tier 1 and Tier 2 factories through factory injury rate monitoring and OHS risk assessment training.
Wage and benefits, living wage, and working hours
Asian sourcing countries have been rated with low scores by the ITUC Global Rights Index.
We support our core Tier 1 factories, with which we have direct business relationships, to provide a fair income for to their workforce, including all legal wages and benefits along with additional components which could increase workers' incomes according to fair wage assessments. We launch fair wage assessments and remediation in collaboration with the Fair Wage Network, for factories which fall short of paying a living wage and continue benchmarking all our core Tier 1 wage data through the Fair Labor Association (FLA) wage dashboard.
We also conduct training on root cause analysis to strengthen working hours management at our core Tier 1 factories, so the level of workers’ income depends less on overtime hours workers.
Child and forced labour
As per World Governance Indicators (WGI), PUMA’s main sourcing countries have been identified as risk countries on Regulatory Quality (RQ) and Rule of Law (RL). The risk could be more upstream in our supply chain when no audit programme is in place or when there is no monitoring programme at the raw material extraction stage. We adopt certification to address raw material extraction and Human Rights risks such as Better Cotton and the Forest Stewardship Council.
In 2021, we conducted a risk assessment on forced labour management through a third party and have prioritised the traceability of our supply chain as a key focus. In addition, PUMA reviewed the severity grading of audit findings according to ILO 11 forced labour indicators to prioritize the remediation process.
risk assessment for new factories
EiQ is a risk assessment tool for new and existing suppliers. The EiQ Sentinel service scans online and media sources and provides alerts for supplier controversies relating to labour, health and safety, the environment, business ethics and management systems. Sentinel alerts provide near-real-time monitoring of supply chains from public news and information sources (in English and local languages), including local or international media, NGO reports, government reports, worker allegations and social media platforms. PUMA checks the EIQ Sentinel whenever it onboards a new factory. For China, we also use the IPE database to check if any of the new factories have a record of environmental violations. We would then ensure that factories comply with PUMA standards though a social audit. In 2023, one factory was not onboarded due to two Sentinel alerts related to potential risks of forced labour.
IPE violations were found in three other factories. One factory was onboarded after it improved as per PUMA standards and corrected its excessive daily wastewater discharge. The second factory improved and passed the legally required environmental assessment but could not be onboarded in 2023 since we had not conducted our social audit, it will be done in 2024. The third factory started production before going through the legally required environmental assessment and without the approval of the local authorities; they improved, so these violations were removed from the IPE database, but they could not be onboarded since we had not completed our social audit within 2023.
For PUMA’s existing supplier factories, 15 Sentinel cases were found as of September 2023. Eight cases were from factories that had already been deactivated, and thus have no production for PUMA anymore. Five cases were related to insufficient payments, health and safety, and waste management, which were addressed through remediation action and the issues were resolved. The other two cases involve allegations that have not been confirmed by our investigations.
risk assessment for existing factories
In 2021, PUMA adopted ELEVATE intelligence (EiQ), a comprehensive suite of supply chain analytics, to:
- Assess our supply chain risks by country, commodity and issue
- Complete risk assessments for suppliers, factories, and sites
- Manage risks that are material to each supplier, factory or site
In 2023, we uploaded 676 audit results (2021-2022) to the EiQ tool. This tool shows the combined risk level based on geography, product, and audit result. We evaluated the countermeasures we have in place in the factories identified as high-risk facilities in this tool. 28 factories were identified as high-risk mainly due to legal violations such as missing building safety permits, systematic excessive overtime or working hours management. 16 factories are from Tier 1 suppliers, one is a warehouse, and 11 are Tier 2 factories. All of them are under regular social compliance monitoring. 29% (eight) of these factories are under the ILO Better Work Programme which offers a factory assessment and advisory services for remediation, 21% (six) of these factories are covered by Worker Voice mobile app, through which workers can raise their concerns to factory management (such concerns are escalated to PUMA when factories do not respond timeously). This mobile app has also the functions to conduct workers survey and launch e-learnings for workers. We also provided Root Causes Analysis training for 25% (seven) of the factories. One supplier in China has been going through a capacity building programme since 2022 at PUMA’s expense to strengthen its management system. In 2023 we saw a significant improvement as per the consultant company Elevate, which we further explained as a case study.
In 2023, 75% (21 out of 28) of factories improved. Measures included obtaining building safety or fire safety certificates, installing sufficient fire safety equipment, and ensuring that emergency exits were unobstructed. Some factories improved working hours management after they joined the Root Cause Analysis training that we provided or paid back insufficient overtime compensation. As a result, these 21 factories are no longer considered as high-risk. The four other factories are still implementing their improvement plan and working to obtain legally mandated certificates and improve working hours management. Three out of four factories have already joined ILO Better Work; for the one factory which is outside of scope of ILO Better Work, we expect them to remedy the critical violations by 2024. The other three factories are to be deactivated.
In 2023, PUMA’s Supply Chain Sustainability Team added one full-time staff member in Brazil. We now have local team members in nearly all high-risk sourcing countries to support the implementation of our standards. In Pakistan, with the launch of the Better Work programme, we have registered all factories in scope to mitigate risks. We plan to add one full-time staff member to support Bangladesh and Pakistan in 2024. For the rest of the high-risk countries such as the Philippines, Mexico, or South Africa, we do not have a local team member due to the total number of suppliers being less than ten. For these locations, we work with third-party auditing firms to conduct regular social compliance audits.
Based on all these actions, we aim to mitigate the risks identified through this risk assessment.
WORKERs SURVEY
In 2020, PUMA launched the Worker Survey Programme to get workers’ feedback in eight countries and to assess their satisfaction with the factory work environment through a mobile survey app.
PUMA operates multiple worker voice channels. The third-party worker engagement platforms cover 89 suppliers and 201,579 workers. 29 non-strategic factories in three countries (Bangladesh, Vietnam and China) also used the platforms in 2023. To review the design and efficiency of PUMA’s grievance system as per the criteria of the UN Guiding Principles on Business and Human Rights, we collected feedback from factory workers in 2023.
The UN Guiding Principles on Business and Human Rights set the following criteria to assess the effectiveness of non-judicial operational-level grievance mechanisms: legitimacy, accessibility, predictability, equitability, transparency, rights-compatibility, a source of continuous learning, and based on engagement and dialogue. In 2023, to assess our hotline against these criteria, we surveyed 14,823 workers at 45 factories in China, Cambodia, Vietnam, Indonesia, the Philippines, Turkey, Pakistan and Brazil.
- Legitimacy (enabling trust from the hotline users): 94% of workers agreed they can trust the PUMA hotline
- Accessibility (no barrier to access for users): 80% of workers know where to find the PUMA hotline phone numbers and email, and 92% confirmed it is available in a language they understand
- Predictability (users are clear on the procedure): 75% of workers responded that they know what the complaint procedure is and 90% understand their complaint will be investigated
- Transparency (keeping parties informed about progress on the issue): 91% of workers with unresolved complaints (at the time they responded to the survey) said they were aware of the status of their cases
The Rights-compatibility criteria (ensuring that outcomes and remedies accord with internationally recognised human rights) was not evaluated. We shall assess it in the future.
The survey results also showed that workers in Brazilian factories did not know where to find the PUMA hotline, nor did they understand the procedure (only 25% responded positive). As a follow-up action, we will conduct further training for workers in Brazil about our grievance mechanism and translate our video material that explains the PUMA hotline procedure into Portuguese in 2024.
Lastly, to evaluate the effectiveness of remedial action, workers were asked systematically whether their complaints were resolved. Of the 15% of surveyed workers who had used the hotline, 65% said they had filed a complaint, with a complaint resolution rate of 96%.
China | Cambodia | Vietnam | Indonesia | Philippines | Turkey | Pakistan | Brazil | Global | |
Can you access a phone in order to call the hotline? | 76% | 93% | 94% | 74% | 92% | 82% | 97% | 66% | 86% |
Do you have access to a phone or computer to send a complaint via email? | 57% | 94% | 92% | 83% | 92% | 85% | 97% | 77% | 82% |
Can you use Zalo, WeChat, Viber, QQ, Whatsapp etc? | 87% | 96% | 97% | 99% | 92% | 97% | 99% | 83% | 94% |
Is the hotline available in a language you understand? | 92% | 88% | 94% | 93% | 98% | 87% | 98% | 89% | 92% |
|
|
|
|
|
|
|
|
|
|
PUMA’s hotline processes and complaints' numbers, statuses and outcomes are publicly available for transparency. Our Rules for the Complaint Procedure is available for download on our website and details about workers and third-party complaints are shared in our Annual Reports. Through regular evaluation of our grievance mechanism, including feedback from factories' workers, we aim to collect information to support continuous improvement of our due diligence and grievance mechanism procedure, in line with these criteria that the mechanism should be a source of continuous learning and based on engagement and dialogue. For equitability, we are seeking to ensure that complainants can access a network of public and private organisations or services to engage through the PUMA hotline on fair, informed and respectful terms. In 2024, we plan to map local relevant organisations and institutions together with our suppliers, to identify and share contacts of emergency care, psychological support or the judicial system, for any factory worker in need who has raised a complaint.
1From 2021 onwards we have used Gallup’s methodology to define the sample of production workers of each factory, based on a 95% confidence interval and a margin of error of plus or minus 5%.
WOMEN’S EMPOWERMENT
Training women about their rights and empowering them to advance their careers is key to achieving gender equality, where both men and women have equal power and opportunities for education, healthcare, economic participation and personal development.
60% of workers producing PUMA goods are women and 50% of factory managerial positions at our core Tier 1 suppliers are filled by women. PUMA initiatives support suppliers in reviewing existing policies and practices or establishing new ones for women’s empowerment. We believe that collaboration within the industry and with NGO experts in women’s empowerment is key to avoid duplication and provide the right expertise.
Since 2021, the accumulated participants of sexual harassment prevention training amounts to 222,933 workers, accounting for more than 148,642 training hours.
In 2023, we expanded the e-learning course on Sexual Harassment Prevention at the Workplace via Micro Benefits to 50,478 workers in 37 factories in China and Vietnam. Another 4,418 workers at eight factories in Cambodia and Indonesia completed the Better Work e-learning course on Discrimination and Elimination of Violence and Harassment at Work via the mobile phone app WOVO, covering 51% of employees in these factories.
China’s textile and apparel industry employs approximately 20 million people, over 60% of them female, comprising many domestic migrants at the age of marriage, childbirth, or childcare. These workers have limited education in personal development, childbirth and family care, and often must juggle their work at the same time. Therefore, the China National Textile and Apparel Council (CNTAC) has launched the initiative to build Family-Friendly Factories in the Chinese textile and apparel industry. This initiative is supported by UN Women and UNICEF. In 2023, we partnered with CNTAC, piloting the Family-Friendly Factories project at three core Tier 1 factories with 5,566 workers in total.
The programme’s objectives are:
- Understand how Chinese textile and apparel companies implement family-friendly policies, as well as their challenges in implementing a gender equality system
- Develop guidance for these companies to promote family-friendly policies at the workplace
- Assist pilot companies in establishing family-friendly mechanisms in line with their existing human resources management system
- Promote and pilot best practices across the industry
In 2023, CNTAC conducted an onsite baseline assessment at three PUMA factories through workers surveys and interviews about their perception of their factory’s current policies and practices, and their challenges regarding family care. The project team also trained 207 workers (73% female) on gender equality, family-friendly policies, work-life balance, and parent-child education. The three factories were provided with an improvement plan to review their internal policies. PUMA’s Sustainability Team is working closely with them to implement these improvement plans by the end of 2024.
PUMA encourages suppliers to join the ILO Better Work programme. The Better Work’s factory improvement process includes three integrated services: assessments, follow-up advisory services and 15 training days per year. In 2023, 32 management staff (72% female participants), from 17 factories in Bangladesh, Cambodia, Indonesia and Vietnam joined 19 training sessions on topics including gender equality, sexual harassment and prevention of discrimination and gender.
The World Benchmarking Alliance (WBA) Gender Benchmark evaluates 112 of the largest apparel, food and agriculture companies globally on their responsibility to drive and promote gender equality in their entire value chain. In the 2023 Gender Benchmark PUMA ranked eighth out of 112 companies and sixth in the apparel sector with a score of 43.5 out of 100. 2023 was the first time PUMA participated in the Gender Benchmark.
Supplier scorecard
In 2023, PUMA conducted calls with 58 core Tier 1 factories to review the social scorecards for each of their factories performance as of end of 2022, which included:
- Audit rating
- Participation in supplementary worker voice tools offered by third parties
- Workers’ training on women’s empowerment/sexual harassment
- Factory's injury rate compared to PUMA core Tier 1 factories’ average rate and 2023 goals
- Factory's average weekly overtime hours vs. PUMA core Tier 1 factories’ average
- Factory’s fair wage performance compared to living wage benchmark
- Whether the factory has freely elected worker representatives against 2025 goals
During these meetings, we reviewed the scorecard and discussed next steps to address identified gaps. Most suppliers agreed with the scorecard and the action plan to achieve PUMA’s 2025 sustainability targets:
- Worker voice: 57 out of 58 factories are covered by third-party worker voice platforms (mobile app) and one supplier in Brazil was added to PUMA’s 2023 strategic partner list. We discussed launching a third-party worker engagement platform. Some suppliers shared their concerns about the functionality of third-party worker engagement platforms, we are looking into it to further improve or find an alternative.
- Fair wage: The discussion was based on the factories 2021 wage data; three factories were suggested to conduct a Fair Wage Assessment as their wage level is below the industry or GLWC benchmark, which was conducted in 2023.
- Women’s empowerment: Except for our new strategic supplier in Brazil, the rest of our core suppliers provided sexual harassment prevention training to workers after the managerial staff had been trained by PUMA. In 2023, 41 out of 58 factories continued the sexual harassment e-learning via the third-party worker engagement platforms, and three Chinese factories joined a pilot led by CNTAC on promoting gender equity.
- Worker representation: During these meetings, we encouraged 20 factories which had not freely elected workers’ representatives, to either join the ILO Better Work programme, which help suppliers to set up a Worker-Management Committee or join PUMA’s programme when the factory is not under the scope of Better Work. Four of them joined the Better Work programme in 2023 or will join in 2024. In 2023, PUMA’s Sustainability Team members in China, Vietnam, Bangladesh and Indonesia had been trained by Timeline Consultancy, a China-based consultancy company, on guiding factories not in scope of the Better Work programme to have freely elected worker representatives and to build a dialogue mechanism. The 16 factories agreed to join PUMA’s Worker Representation Programme.
SOCIAL COMPLIANCE
PUMA’s Code of Conduct is an integral part of our supply contracts. All PUMA suppliers sign a legally binding “Declaration of Principles” to comply with the PUMA Code of Conduct. PUMA requires all vendors, their subcontractors, and their suppliers to comply with this Code of Conduct, as well as PUMA’s Social and OHS handbooks. These compliance expectations are verified through regular audits. The frequency of audits is based on a factory’s previous audit results: A-graded factories are re-audited after 24 months, B+ after 18 months, B- after 12 months and C-graded after six months. Warehouses graded A, B+, B- are re-audited after 24 months, C-grade after 12 months and D after six months. For factories with a D grade, including Better Work Factories, Zero Tolerance (ZT) issues need to be corrected between two and six months. Potential new factories will not be authorised to produce PUMA products until the factory can be rated A or B. Regardless of the factory grade, all issues identified during audits need to be remediated as part of a corrective action plan.
Since 1999, all direct PUMA factories (Tier 1) have been frequently audited for compliance with the ILO Core Conventions and basic environmental standards. Each year we collect between 300 and 500 audits or assessment reports issued through PUMA’s compliance programme, the ILO Better Work Programme, our industry peers’ compliance programmes or independent experts accredited by the Social and Labour Convergence Programme (SLCP). We have also included our most relevant material and component suppliers (Tier 2) and key priority warehouses in our audit programme. Through collaborative efforts with the sourcing team, we mapped more than 200 non-core Tier 2 suppliers in 2022. While one-third use FEM (Facility Environmental Module) for other brands, only 13 have had a social audit. We converted these audit reports in our grading system. In 2023, we reminded all suppliers that the use of undeclared sub-contractors is a Zero Tolerance issue, as per PUMA standards. We asked them to self-declare their Tier 1 subcontractors used for PUMA production. 66 Tier 1 subcontractors were declared, 26 (19 for the first time) had an audit report that we converted into PUMA‘s grading system.
In 2023, 454 Tier 1 suppliers, 92 Tier 2 suppliers and three warehouses were audited. 581 audit reports from these 549 factories were collected to safeguard workers’ rights to more than half a million workers (656,473).
All PUMA suppliers are required to display our Code of Conduct in factories producing PUMA products, materials or components. This contains the contact details of the PUMA Sustainability Team as a whistle-blower hotline. The number of grievances received and solved, as well as the most frequent type of grievances are shared in this report.
Furthermore, PUMA is a member of the Fair Labor Association, which regularly audits and accredits PUMA’s compliance programme for compliance with the Fair Labor Association’s Code of Conduct. This ensures that PUMA has the systems and procedures in place to successfully uphold fair labour standards throughout its supply chains and mitigate and remediate violations. As an FLA member, PUMA has agreed to subject our supply chain to independent assessments and monitoring as part of an organisational commitment to upholding fair labour standards through transparency. FLA publishes the results of these assessments to encourage an open and honest dialogue about the conditions that workers face, ensure PUMA’s accountability, and help consumers make more informed decisions about the products they buy. View the public assessment results here: PUMA, SE – Fair Labor Association.
A comprehensive explanation of our compliance programme for suppliers (including grievance mechanisms and case studies) can be found in our Sustainability Handbook for Social Standards. Our Social Handbook explains the procedure for factory monitoring programmes (section 3) and our standards. This handbook is reviewed on a regular basis and our suppliers receive regular training on our standards and monitoring process. We launched the e-learning via Elevate’s EiQ Learning platform in April 2023. All suppliers were invited to complete the training course. 1,035 participants from 557 factories passed the e-learning in 2023, representing 85% of PUMA’s active factories.
PUMA’s supplier factory list is disclosed on our website. It includes details such as the factory name, address, product category, headcount range, the percentage of female workers, percentage of foreign migrant workers and freely elected worker representation. PUMA also publishes its factory list in the Open Supply Hub platform.
Audit process
Our audit starts with briefing the factory management and worker or union representatives on PUMA standards, the audit process and its scope. In 2023, 94% of the audits conducted included a trade union representative or workers’ representative during the audit’s opening and closing meetings (when closing meetings take place during factory working hours).
We have a team of compliance experts in all our major sourcing regions who regularly visit our core manufacturing partners. We work with external compliance auditors and with the ILO’s Better Work Programme. Each PUMA supplier factory must undergo a regular compliance audit every six to 24 months based on their audit rating and all issues identified need to be remedied as part of a corrective action plan.
Interviews with workers, workers’ representatives or union representatives are crucial for understanding workers’ perspectives on workplace standards, the atmosphere at factories and protecting vulnerable workers from any work that is likely to cause harm. All interviews with workers are conducted on-site (no offsite interviews).
Around 79% of active factories were audited in 2023. Factories not audited in 2023 either had an audit that was still valid because of their grading, were waiting for Better Work assessment or were located in Ukraine.
To avoid duplication and prevent auditing fatigue, in 2023, we increased the percentage of shared assessments to 67% (59% in 2022). We will further increase our use of SLCP-based assessments to 350 factories in 2024. We believe that SLCP is an ideal tool for building long-term relationships with suppliers and supporting them to take ownership of their social and labour data. PUMA is a member of the ILO Better Work Programme and uses Better Work assessment reports in lieu of the PUMA compliance programme. PUMA also uses FLA-accredited brands' reports as well as some other brands’ audit reports in lieu of the PUMA compliance programme. We aim to use external reports converted to PUMA standards for up to 80% of our factories by the end of 2025.
2023 | 2022 | 2021 | |||||||
T1 | T2 | Warehouse | T1 | T2 | Warehouse | T1 | T2 | Warehouse | |
A (Pass) | 120 | 24 | 63 | 17 | 75 | 6 | |||
B+ (Pass) | 154 | 27 | 1 | 157 | 41 | 144 | 23 | 2 | |
B- (Pass) | 152 | 38 | 2 | 144 | 39 | 2 | 155 | 46 | 1 |
C (Fail) | 18 | 2 | 19 | 11 | 1 | 16 | 7 | ||
D (Fail) | 10 | 1 | 9 | 4 | 3 | 2 | |||
Total Active+Inactive audited factories | 454 | 92 | 3 | 392 | 112 | 6 | 392 | 82 | 3 |
Total active factories as of Dec 31st, 2023 | 564 | 120 | 7 | 516 | 128 | 10 | 445 | 99 | 6 |
Number of employees | 572,541 | 81,756 | 2,176 | 546,286 | 82,070 | 2,229 | |||
Audit coverage % | 80% | 77% | 43% | 76% | 88% | 60% | 88% | 83% | 50% |
Total active+inactive audited factories | 549 | 510 | 477 | ||||||
Pass/Fail % | 94/6 | 97/3 | 100 | 93/7 | 87/13 | 33/67 | 95/5 | 91/9 | 100 |
|
|
|
|
|
|
|
|
|
|
↗ G.07 AUDIT RESULTS 2021 – 20231
1Total factories audited: 477 in 2021; 510 in 2022; 549 in 2023
Audit results and findings
In 2023, we continued following up and training the factories with low performance; as a result, 67 factories were upgraded to A or B+. 144 factories were audited for the first time in 2023 as per our strategy to increase local-for-local production and to scale up our social monitoring programme to non-core Tier 2 suppliers (11) and Tier 1 sub-contractors (19).
In total, 36 factories failed the audit, (31 Tier 1, five Tier 2); 14 were deactivated due to low performance. Five were re-audited in 2023 and passed the audit; 17 factories will be re-audited in 2024 since they have six months to improve. 19 out of 36 were new factories, 12 factories were not onboarded so we did not enter into any business relationship with them, four were re-audited and improved to a passing grade, the three other factories (two non-core Tier 2, one retail furniture supplier) were audited for the first time in 2023 as we expanded our audit scope; they all committed to improve and they will be re-audited in 2024.
Out of the 11 factories graded D in 2023, seven factories were deactivated. Four are still active as at the end of 2023, as progress is on-going. Two out of these four D-graded factories had Zero Tolerance issues on transparency and payment below minimum wage which were uncovered in late 2023. They corrected these issues within 2023, as one paid back minimum wages. The other factory stopped subcontracting home workers, recruited workers and communicated their policy change to all managerial staff and workers; several critical issues are still under remediation and should be corrected in 2024. For the other two D-graded factories, since the factory management submitted reliable corrective action plans, we will follow up on the remediation by mid-2024.
↗ G.08 2022-2023 NUMBER OF MOST FREQUENT FINDINGS1-2
1Top 10 findings in 2023 active factories only excluding newly audited factories in 2022 and 2023
2Including converted reports
G.08 shows the 10 most frequent audit findings from PUMA’s audit programme, including both own and external converted reports.
Initial assessments are excluded from this graph. 144 audits were initial assessments (meaning no audit was conducted previously) in 2023, 25% of the total number of audits performed over the course of the year. These suppliers are not yet familiar with our standards. In 2023, we provided an e-learning on our social standards, which helped newly onboarded suppliers to better understand our expectations. As a result, the pass rate of newly onboarded suppliers in 2023 was 4% higher than in 2022 (2023: 87%; 2022: 83%).
Working hours management: In 2022 we provided working hours management training for all Tier 1 factories. A root cause analysis workshop was held with selected core suppliers in both 2022 and 2023 to explore opportunities for improvement. Factory management reviewed and strengthened their policy and working hours monitoring system. They gained a deep understanding of how to conduct a root cause analysis. We developed an action plan to address prioritised root causes of overtime hours. We noticed improvements as there was a decrease in the number of audit findings in systematic excessive overtime (reduced by 4.6%), overtime compensation (reduced by 3.2%), and working hours management (reduced by 0.6%). We notice a decrease in the average overtime hours at our core Tier 1 factories compared to 2022 from 7.7 to 5.3 hours in 2023, but it can be due to a decrease of our order book due to 2023 global macroeconomic situation, which led to a change in customers' ordering behaviour.
Wages and overtime: Among issues related to wages and/or overtime, 31% of the corrective actions were implemented and these issues were resolved in 2023, which is 20% higher than the 11% rate in 2022. We expect more progress in 2024 as 31% of audits were conducted at the end of 2023, these factories involved will receive a follow-up audit in 2024 to validate their improvements.
Social security: 100% of workers are covered under social security among all our core Tier 1 suppliers, except in China where this is the case for 80.4% of workers. We plan to further explore how to support suppliers to remedy those issues via in-person workshops in 2024. Improving working hours management, following up with suppliers to obtain legal permits, and increasing social security coverage will continue to be a focus of our efforts.
Transparency: Four transparency issues were found in 2023. One new factory with one transparency issue along with other violations such as insufficient benefits and several OHS findings was not onboarded as a PUMA supplier; two factories with one transparency issue each provided consistent records for review after we emphasised PUMA’s zero tolerance policy on transparency. These records were verified by PUMA. One transparency issue in one factory detected in late 2023 remains open; we will follow up in early 2024.
Freedom of association: The four open issues related to Freedom of association identified in 2022 were all closed through follow-up with the management or under the Better Work programme. Five audit findings related to Freedom of Association breaches were identified in 2023, such as the dismissal or poor treatment of union members and delayed union elections. As of today, three issues were closed; one is still open as there is an on-going mediation process between the management and trade union workers; the other issue remains open, and concerns the factory HR manager taking dual leadership roles in both management and union. This factory is working with Better Work Vietnam for remediation.
Women’s rights: PUMA is committed to respecting women’s rights as per the Convention on the Elimination of Discrimination Against Women and expects suppliers to commit to and respect women’s rights. In this context, we carefully monitor working conditions for women. In 2023, we identified 38 women-related audit findings about missing benefits for nursing workers, unadopted conditions for pregnant workers or toilets not maintained in clean and sanitary conditions. 15 of them were closed through follow-up with the factories or via the Better Work programme, three findings will not be followed-up on because the factories have been deactivated, 20 are still under remediation and are being followed-up. One violation was related to unvoluntary overtime and has been corrected as per a Better Work progress report.
Freedom of movement: One audit finding was identified related to restricted freedom of movement. As a result, the factory management issued warning letters to all relevant supervisors and conducted training to avoid similar situations in future. We will verify these actions onsite in 2024. No case was found related to workers' passports nor other identity and personal documents being retained.
Wage payments: We identified 16 violations regarding delayed wage payments, 12 of them were closed; two findings will not be followed-up because the factories were deactivated; for the two open findings, one factory is working with Better Work on remediation, and another factory took appropriate actions so no wage payments will be delayed. We will verify that proper actions were taken on-site in 2024.
Beyond auditing, we track social key performance indicators such as average payments vs. minimum wage payments, overtime hours or coverage by collective bargaining agreements. This data is reported under the Fair Income target section.
Supplier Training
To ensure that our suppliers understand the requirements set by PUMA as well as international due diligence regulation and standards in the garment and footwear industry, PUMA organised multiple training sessions in 2023, including:
- In-person or virtual suppliers round tables to share updates on PUMA standards and industry best practices, elaborate on the German Due Diligence Supply Chain Act by industry experts; CNTAC in China and VITAS in Vietnam.
- Training factory management on Accident Prevention and Reporting, who will then support us to achieve the goal of training 100,000 workers on this subject.
- Root cause analysis training for strategic suppliers, so that they can develop corrective actions to resolve their audit findings by addressing their root causes.
- Customised e-learning on Social Standards, to help suppliers, especially those newly onboarded, to better understand PUMA's expectations.
- PUMA’s expectations to suppliers regarding our Code of Ethics.
We launched the e-learning via Elevate’s EiQ Learn platform in April 2023, and all suppliers were invited to complete the training. 1,035 participants from 557 factories passed the e-learning in 2023, representing 85% of PUMA’s active factories. We plan to add this e-learning to PUMA’s website, which will allow users, new factories and workers, to access the course at any time.
Topics | Number of factories | % of suppliers trained* | Number of participants | |
Supplier in-person round table or virtual meetings | Sustainability updates, best practices sharing, German Supply Chain Act. etc. | Average. 532 per round | 81% | Average. 1,122 per round |
Code of Ethics** | 536 | 82% | 1,230 | |
OHS Accident Prevention and Reporting training | Training of Trainer to core Tier 1 supplier management on what and how to do OHS Accident Prevention and Reporting | 102 | 16% | 290 |
Root Cause Analysis training | In depth review of root cause analysis methodology to new core Tier 1 and core Tier 2 factories | 71 | 11% | 169 |
PUMA Social Standards e-learning | PUMA social standard handbook e-learning course via EiQ Learn platform to active factories’ management | 557 | 85% | 1,035 |
|
|
|
|
|
*% of factories joined the training based on total 656 factories. The 656 factories include PUMA core Tier 1 and Tier 2, non-core Tier 1, stichd factories and licensee factories.
**Included to second supplier in-person round table or virtual meetings.
Capacity Building in ChinaWith Elevate as a partner, a one-year capacity building programme was carried out to help the supplier and its factory staff to identify key gaps in the factory’s management system and provide them with a toolkit and expertise to drive sustainability-related improvements. Through top management commitment, training and capacity building, regular review of metrics and impact assessments, the factory understood the importance of being transparent with PUMA; established a proper grievance mechanism, established an effective working time recording system; started to use internal inspection tools to manage CSR performance independently and corrected most (91.7%) of the EHS findings. To further improve it was recommended that the factory should enhance compensation and benefits payment systems, conduct follow-up investigations of workers’ suggestions and have a proper mechanism to answer these suggestions. |
Grievance Channels
PUMA works towards providing access to functioning grievance channels throughout its supply chain. Where we do not have direct operations, we seek out partners who can run such complaints mechanisms, according to the UN Guiding Principles. At the cotton farm level, the Better Cotton Grievance procedure provides a system for anyone, including third parties, who engages with its activities, people or programmes to raise a complaint relating to any aspect of Better Cotton and its activities.
We operate multiple worker voice channels to reach more than half a million workers at our Tier 1 and core Tier 2 factories. If workers are not satisfied with the responses offered by the factories via their respective internal grievance system, we encourage them to use the PUMA hotline to raise complaints or request consultations. Hotline contact details are published on our Code of Conduct posters, displayed at every audited factory globally. We also use WeChat, Zalo, Facebook and other social media channels to connect with workers and have established more formalised compliance and human resources apps at selected core suppliers.
The third-party worker engagement platforms cover 89 factories (201,579 workers), which represents more than 80% of our production volume. In 2023, 1,544 feedback messages were received through the MicroBenefits and the WOVO platforms in China, Indonesia, Pakistan, Philippines, Turkey, Cambodia and Vietnam, as well as the Amader Kotha Helpline in Bangladesh. Of the 1,544 messages, 41 cases were escalated to PUMA as the factory did not respond within the 48-hour timeline. PUMA engaged with the factories’ management to address workers’ concerns. All other concerns not escalated to PUMA were handled and resolved directly by the suppliers.
In 2023, we engaged with a local hotline, Hamari Awaz who will provide all workers in factories producing for PUMA in Pakistan with access to a local hotline in early 2024.
In 2023, 107 workers’ concerns were raised through PUMA’s hotline across eight countries. Together with our suppliers, our team was able to resolve all these cases.
In 2023, to meet its obligations under the German Act on Corporate Due Diligence Obligations in Supply Chains (LkSG), PUMA published its Rules for the Complaint Procedure. PUMA’s own employees and the employees of PUMA’s business partners can submit complaints in connection with human rights or environmental risks and violations, as well as violations of PUMA policies via the following channels:
- PUMA’s electronic whistleblowing platform
- Telephone numbers of the PUMA Sustainability Team (“PUMA Hotline”)
- Third-party platforms made available to factory workers by the factories
Complaints may be made anonymously and all information regarding the complaint is treated as strictly confidential and only shared on a need-to-know basis or if required by law. All complaints received are acknowledged within seven days and PUMA shall conduct a comprehensive investigation without delay. PUMA will also share the outcome of the investigation with the party making the complaint.
PUMA shall review the effectiveness of its complaint procedure at least once a year, or on an adhoc basis if PUMA expects a significant change or increase in risk exposure in PUMA’s own operations and at PUMA’s business partners. We aim to translate the Rules for the Complaint Procedure into 40 languages in 2024 to ensure it is accessible for end users in PUMA’s supply chain.
2023 | 2022 | 2021 | 2020 | |
Total received – external channels (third-party platforms) | 1,544 | 2,006 | 3,132 | 1,021 |
Total received – PUMA Hotline | 107 | 159 | 223 | 101 |
Total confirmed- PUMA Hotline and third-party platforms | 1,443 | 1,877 | 3,165 | 984 |
Total received – PUMA Hotline and escalated to PUMA via third-party platforms | 148 | 173 | 262 | 127 |
Resolved - PUMA Hotline and escalated to PUMA via third-party platforms | 148 | 172 | 261 | 126 |
Not resolved - PUMA Hotline and escalated to PUMA via third-party platforms | 0 | 1 | 1 | 1 |
Resolved (%) | 100% | 99.4% | 99.6% | 99.2% |
|
|
|
|
|
↗ G.09 NUMBER OF MOST FREQUENT GRIEVANCES RAISED IN 2023 THROUGH PUMA HOTLINE AND THROUGH THIRD-PARTY PLATFORMs ESCALATED TO PUMA
worker complaints
The most frequent areas of concern raised by workers remain as fair compensation, their employment relationship, and excessive working hours. Most workers’ concerns about wages and benefits are mainly due to their misunderstanding of wage and benefit calculations. We asked factories to proactively talk to and train workers on wage and benefits' calculation methods. Regarding the employment relationship topic, many cases are about workers wishing to resign without following the legally required notice period. We asked factory management to discuss solutions with their employees.
In any country, when workers complain about working during public holidays or overtime hours, PUMA would engage with factory management, to adjust the production schedule and to make sure overtime is voluntary and properly communicated with workers. Furthermore, PUMA provided training to these factories on working hours management, and overtime root cause analysis to prevent excessive overtime.
Below is a case study of the PUMA Hotline, which explains how we followed-up with our supplier to close the single remaining open case of 2022.
PUMA HotlineA worker from a footwear factory in Vietnam called the PUMA Hotline in September 2022 regarding the subsidies sponsored by the government according to the Resolution No. 68/NQ-CP dated on July 1st, 2021. Under this regulation, employees who were under contract suspension or termination, or unpaid leave between May 1st, 2021 and December 31st 2021, and pregnant or taking care of children under six years old are entitled to one of government subsidies. The complainant submitted all the necessary documents to the factory to apply for this government subsidy but did not receive any updates. PUMA immediately contacted the factory. The factory explained that due to being busy with Covid prevention measures and high levels of absenteeism in January 2022, they missed the deadline to submit the documents to the local authority. In total 2,032 workers failed to receive a total amount of about $ 115,000. Despite the factory’s efforts to follow-up with the local authority for the payment, there was no positive response. |
THIRD PARTY COMPLAINTS
We continued following-up on the six open third-party complaints in 2022. Five related to freedom of association were resolved through active engagement with factories, union and other stakeholders, with union representatives reinstated or compensated in agreement with the unions involved. One of these five cases was settled in collaboration with the Fair Labor Association and other brands, more details can be found in case study below. Another complaint is about workers’ wages in Mauritius, which was followed-up under the umbrella of the Fair Labor Association and in collaboration with other brands: migrant workers in Mauritius received less than a minimum wage after the dormitory fees were deducted from their salary. Based on the inspection report of local labor authority the practice is legal. In 2024 we will continuously engage with the FLA and other stakeholders to find a collective solution.
In 2023, we received 15 third-party complaints from external organisations, 11 of which have been resolved.
Nine cases were related to freedom of association breaches, eight out of these nine cases were resolved through active engagement with factories, unions and other stakeholders. The union representatives were either reinstated or compensated in agreement with the unions involved. One case is still going through the mediation process between management and the trade union.
Three cases involved wage and benefits issues; one of them is the request from the Bangladesh Union Federation to provide support on their minimum wage demands. Upon receipt, PUMA actively engaged with ILO Better Work and the Fair Labor Association. We published our Position on our website, and co-signed a letter to the prime minister with other brands, through Fair Labor Association in November, to support trade unions. Another two wage and benefits cases are still under investigation.
Two cases relate to NGO reports on working conditions for supply chain workers in Pakistan and Cambodia. For both reports we engaged with ILO Better Work and the reporters. Details are provided under Pakistan and Cambodia paragraphs below.
In May 2023, a trade union requested the dismissal of two managers at a factory in Cambodia because they thought they were responsible for the reduction of orders, among other concerns. The management and union had several meetings to discuss the concerns. The management accepted all the trade union’s concerns and took action, except for the dismissal of the two factory managers, which the trade union agreed to retract.
Pakistan
In 2023, Labour Behind the Label published a Report on labour rights in Pakistan regarding issues such as no payment of living wage, no employment contract, leave being denied or unpaid, child labour, no social security, harassment, health and safety issues, fire safety risks and freedom of association breaches.
PUMA has investigated the details of the report and engaged with the reporters to understand the methodology used. The report relates to factories located in Karachi, Faisalabad, and Lahore. While PUMA does not have a business relationship with any suppliers in these regions, our subsidiary stichd, does have a business relationship with four factories in this region, two of which are included in the report.
Three out of the four factories in the mentioned areas were audited in 2023, while one factory was audited in 2021 with a rating still valid in 2023. As a follow-up in 2023, PUMA conducted a full unannounced assessment of all four factories through a different third-party company. As a result, three of the factories were downgraded. We are closely following up on progress to address these newly identified violations and all factories producing PUMA products that fall within the scope of the Better Work programme are now enrolled in the Better Work programme. Additionally, all workers of factories producing for PUMA in Pakistan will have access to a local hotline, Hamari Awaz.
Better Work Pakistan will also provide a social dialogue programme, as well as leadership capacity building initiatives and training for female workers. Other services will include the ILO’s occupational health and safety approaches, a factory improvement toolkit and productivity focused training. Additionally, PUMA signed the ACCORD Pakistan in March 2023 for all factories producing PUMA and stichd products.
Cambodia
In 2022 we received five complaints concerning three Cambodian factories, about potential breach of freedom of association rights. Three were resolved in 2022 and two in early 2023. We worked to find the best solution related to these concerns, facilitating mediation meetings between workers’ representatives and factory management, partnering with Better Work Factories Cambodia and/or with other brands producing in the same factories. It took three to five months to solve these complaints.
Despite all our efforts, we received five complaints about freedom of association from Cambodia in 2023. Four cases were resolved through open dialogue and facilitated mediation meetings between factories and unions. One case is still under mediation or investigation.
We continued to work with Better Factories Cambodia (BFC) and hosted a training series from April to August 2023 for all Cambodian factories producing PUMA products. 183 participants from 27 factories’ management teams, shop stewards and union representatives attended the training. As a lesson learned from training conducted in 2021, we added one exclusive session for factory decision-makers in Chinese in addition to a session conducted in Khmer for workers representatives and trade union leaders.
The aim of the training was to provide participants with a better understanding of:
- Rights and obligations of the employer, unions and worker representatives
- Managing communication and employment contract termination such as: resignation, dismissal, and retrenchment.
As per the BFC feedback, as result of the training participants confirmed they gained a better understanding about Freedom of Association and their roles and responsibilities. All 27 factories submitted a Corrective Action Plan after the training. We will verify the implementation of each action plan in early 2024 according to the five KPIs established by BFC. They are described below:
1.Conduct regular meetings between the employer, union and shop stewards to raise and address any concerns in the workplace on weekly/biweekly/monthly basis.
2.Develop/review a Freedom of Association (FoA) policy in consultation with the unions and shop stewards and implement this policy accordingly.
3.Develop/review a Grievance Handling policy in consultation with the unions and shop stewards and implement this policy accordingly.
4.Develop/review a policy for Employment Contract Termination in consultation with the unions and shop stewards and implement this policy accordingly.
5.Provide internal/external training to more workers on relevant topics such as the roles and responsibilities of the employers, unions and shop stewards.
In September 2023, the NGO Action Aid published an investigative report alleging that garment factories in Cambodia, supplying apparel and footwear to companies (including PUMA), reduced monthly wages compared to 2020 levels and failed to pay sufficient severance when the factories closed due to the COVID-19 lockdown. The report, which interviewed 308 garment workers in 15 factories, also claimed that workers were unable to afford necessities even after the COVID-19 lockdown restrictions were lifted due to lower wages and fewer overtime hours, while overtime pay became a systemic dependency.
Following the report, PUMA engaged with the Clean Clothes Campaign (CCC) and Action Aid to understand the methodology behind the allegations that were made. For PUMA, the allegations relate to six of PUMA’s suppliers, two of which PUMA had ended the business relationship with by mutual agreement in 2021. After further investigation, PUMA did not identify any wage gap as per the government’s instructions during the lockdown period in the remaining four factories. Although “no work, no pay” directives were in effect, PUMA ensured that workers would receive a regular income during 2021 lockdown through regular communication with our suppliers in collaboration with our sourcing team.
Between 2019 and 2022, Cambodia represented around 13% of PUMA’s total sourcing volume. In 2020 and 2021, PUMA focused on keeping suppliers in business and safeguarding workers’ health, employment, and income through several measures including: minimizing order cancellations (0.35% of orders were cancelled in 2020) and expanding our PUMA Vendor Financing Programme, with an increase in suppliers' participation from 21% in 2019 to 30% in 2020. As a responsible business partner for our suppliers, PUMA set up a responsible purchasing practices policy and engaged with Better Buying, an independent non-profit organisation, to collect feedback from our core suppliers related to our purchasing practices. We reported the key findings of the Better Buying survey in this report.
Indonesia On July 7th, 2023, PUMA received complaints from a union related to union staff members at one of PUMA’s footwear suppliers who were terminated based on not passing their probation period. The union mentioned that the termination was considered illegal since it was without prior notice and no evaluation was performed by a respective supervisor and section manager. The union believed that this happened due to their union membership. The union leaders asked PUMA to support the reinstatement of the three workers. On July 13th, 2023, PUMA investigated and interviewed the factory management and union representatives. PUMA found that the termination of the three union members was not legal since there was no clear performance assessment from the respective of the section heads. This was explained to factory management who agreed to re-instate the three workers to the same position with the same wage. No wages were deducted for the period when the workers were laid off. The union leader acknowledged PUMA’s engagement in this case and recognised our commitment to respect freedom of association. Madagascar In June 2022, PUMA received a request from IndustriALL’s Sub-Saharan Africa regional office to support one of their trade union affiliates called SEMPIZOF in Madagascar. According to IndustriAll, about 350 machinists went on strike in a factory producing for PUMA and other brands from May 18th to 25th, 2022 to protest on wages and unfair skills’ assessments for experienced workers. The strikers also denounced sexual harassment against female workers and bribery during recruitment. SEMPIZOF approached the Labour Inspectorate and Labour Tribunal with another IndustriALL affiliate SVS to request the reinstatement of 50 workers (dismissed during the strike) and respect of workers’ rights. We immediately followed up with the supplier, who confirmed the unrest of 345 workers (out of 1,550), the dismissal of 58 workers, and their willingness to collaborate for remediation. The four brands including PUMA producing in this factory had several meetings on collaborative actions and reached out to the Fair Labor Association (FLA) for support. In July 2022, during a first call with the FLA, the brands agreed to find an independent third party to conduct an in-depth investigation. The FLA interviewed several candidates and commissioned an independent third-party The Labour Hive in November 2022. It completed an investigation and provided a detailed report with suggested actions in February 2023. The report includes a thorough analysis of all allegations. The factory immediately suspended the manager related to sexual harassment allegations and dismissed him after the investigation. The investigation did not identify issues related to overtime, short-term contracts, unfair dismissals because of trade union activities nor bribery at recruitment. The FLA published the results of the investigation report. Brands studied the report and agreed on an action plan with the supplier in May 2023. During a follow-up verification of the remedial action plan in November 2023, it was confirmed and verified by The Labor Hive that factory management had engaged with various stakeholders such as local authorities, Better Work, trade union (FISEMA), and worker reps to take corrective actions. Various projects and programmes have been implemented, and improvements such as an increased meal allowance, adjusted salary as per government decree, regulating probation period for production workers, and removal of the dismissed workers from the blacklist (so that they can find jobs in other factories) were made. In partnership with ILO Better Work, the factory arranged several trainings on Freedom of Association, Harassment and Abuse, Compensation and Benefits and Hours of Work. Further improvements on workplace dialogue, workers’ satisfaction surveys, training effectiveness, renewal of workers’ representation election, and the implementation of a workers’ performance evaluation system are still on-going and aim to be completed by August 2024. |
ZERO TOLERANCE ISSUES
All issues identified during our auditing and hotline activities are classified as zero tolerance issues (such as child labour or forced labour), critical issues or other issues in our Sustainability Handbooks.
Zero tolerance issues lead to the immediate failure of an audit. If these issues are reported for a new factory, the factory will not be allowed to produce PUMA goods. Established suppliers must remedy all zero tolerance issues immediately by conducting a root cause analysis and implementing preventive measures to prevent the issue reoccurring. As a last resort, a business relationship can be terminated if the factory fails to cooperate. Other issues are also followed up on by our Compliance team.
In 2023, we identified 19 zero tolerance issues and were able to remedy eight on workers’ compensation in line with legal requirements, lack of transparency and wastewater discharge. Two zero tolerance issues remain open. One was related to a South Africa-based factory producing furniture for our retail stores paying 94% of the minimum wage, as they were granted an exemption by local authorities. After meeting the factory management, they committed to pay the full minimum wage from July 2024. Another example is a factory in Pakistan which was found to have transparency issues during an unannounced audit in late 2023 conducted after the publication of a Report from Labour Behind the Label. The factory committed to improve and joined the Better Work programme in December 2023. We informed Better Work about this case and intend to resolve this issue during its first assessment. Nine factories were not onboarded or were deactivated in 2023. The increase in zero tolerance issues is due to the increased number of factories audited in 2023.
2023 | 2022 | 2021 | |
India | 5 | 3 | |
Bangladesh | | 3 | 2 |
Cambodia | 2 | 1 | 2 |
Vietnam | 2 | 2 | |
Canada | 3 | | |
Pakistan | 2 | | |
South Africa | 2 | | |
Brazil | 1 | | |
China | 1 | | |
Egypt | 1 | | |
Malaysia | | 1 | |
Philippines | | 1 | |
Spain | | 1 | |
Grand total | 19 | 12 | 4 |
|
|
|
|
FREEDOM OF ASSOCIATION PROTOCOL IN INDONESIA
To ensure workers’ voices are heard, we want to foster Freedom of Association (FoA) and signed the Indonesia FoA Protocol.
The main objectives of the Freedom of Association Protocol are:
- Eliminate the practice of union busting in the factory and to foster healthy industrial relationships
- Factory management and union leaders can identify violations and challenges around FoA that arise in the factory and are able to discuss solutions together
- Avoid victimisation of union representatives and members when disputes arise between union members and management
- Set up fair rules for the implementation of FoA by having a joint understanding and commitment between workers and the factory management
- To have extra layer of rules and regulations related to FoA practice that is not regulated in Law No. 21/2000
As of end of 2023, seven Tier 1 factories have agreed to apply the FoA Protocol with 13 unions. Two factories are planning to sign up in 2024, while the remaining ten Tier 1 suppliers either do not have a union or their union is not a member of FoA Protocol. As of end of 2023, no FoA case within PUMA suppliers has been escalated to the FoA Protocol national committee. FoA cases are mainly resolved internally at a factory level without PUMA’s involvement.
WAGE ISSUE IN KARNATAKA
On February 19, 2020, the state government of Karnataka increased the Variable Dearness Allowance (VDA), requiring manufacturers to pay workers Rs. 417.56/month as a component of their wages, from April 2020 onwards. The VDA is calculated based on the increase or decrease in the consumer price index (CPI) to help employees in the public and private sector to cope with the rising cost of living due to inflation.
The Karnataka labour department deferred the payment of VDA (as per the VDA Hike Order) until March 2021 due to the financial hardships caused to employers during COVID-19. Two unions challenged the deferral order and filed two petitions in August 2020. On September 11, 2020, the Karnataka High Court announced that the Labor Department’s postponement of the wage increase was illegal as per Section 26(2) of the Minimum Wages Act. This means that non-payment could be seen as being in contempt of such a court order. In practice, factories paid Rs. 622.44/month VDA to workers from April 2021, but they did not pay Rs. 417.56/month to workers from March 2020.
We have actively been working with our sourcing and suppliers in the region, informing our three suppliers that PUMA expects suppliers to pay the incremental minimum wages (considering both the 2020 and 2021 VDA adjustment), including arrears to both existing and former workers. We aligned our expectations of suppliers with the Worker Rights Consortium and kept informing them on our progress. In 2023, $ 484,928 was paid to 13,687 workers, including both existing and former workers. We verified payment on-site, except for one factory onboarded in April 2023, where a visit is scheduled in early 2024.